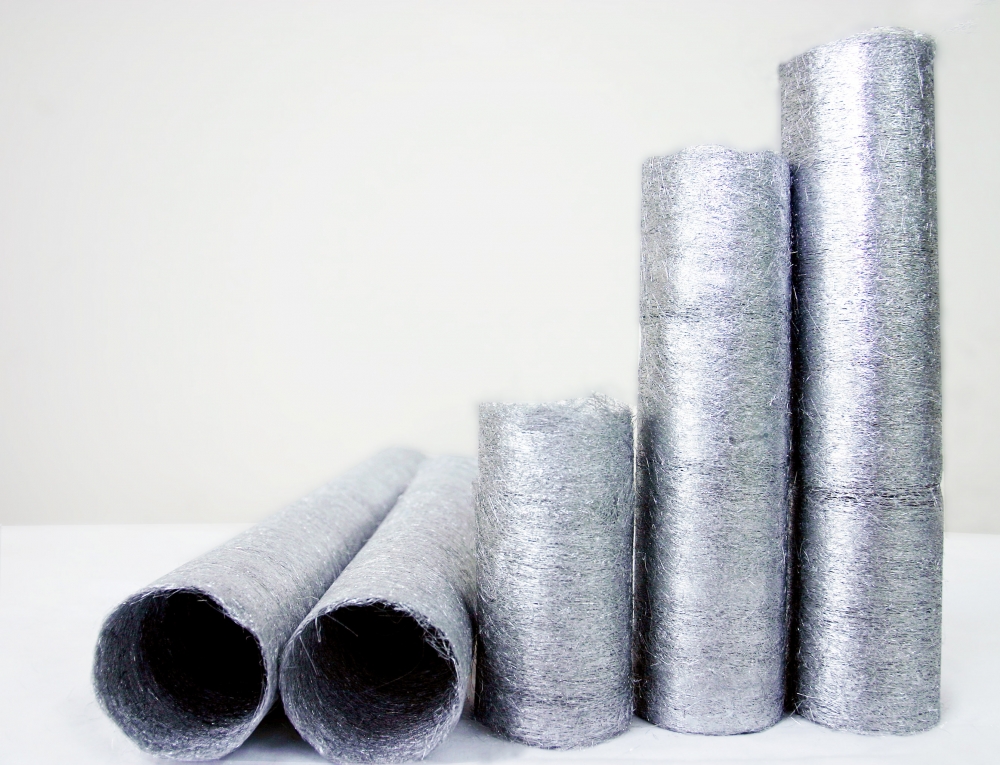
국내 산학 공동연구팀이 기존 제품의 10분의1 가격수준으로 양산할 수 있는 알루미늄섬유 부직포 기술을 개발했다. 그동안 외산제품에 의존해온 알루미늄섬유 부직포는 주로 소음을 줄이기 위한 흡음재나 전자파 차폐, 광촉매 필터, 자동차용 필터 등에 주로 사용되는 고기능성 소재로 이 제품이 상용화되면 연간 100억원이상의 수입대체효과가 기대된다.
한국산업기술대 신소재공학과 연구팀과 알팩(대표 박부근)은 고주파 처리한 알루미늄 판재에서 초극세 섬유를 추출, 접착제를 사용하지 않고도 자체 열로 소결(단단히 뭉치는 현상) 접합이 가능한 부직포 제조 기술을 개발했다고 7일 밝혔다.
지난 2년간 개발된 이 기술은 섬유 제조·절단·성형·소결 등 복잡한 공정을 거쳐 섬유와 섬유 사이를 접착제로 붙이는 방식의 기존 일본 등 외산제품과 달리 접착제를 사용하지 않고도 고온에서 접합이 가능하다. 이에 따라 내습성이 크게 높아지며 생산공정 단축과 가격 경쟁력 제고 효과가 크다고 연구팀 측은 설명했다.
부직포에 사용되는 알루미늄섬유는 머리카락 굵기의 3분의1에 불과한 20미크론(㎛) 정도로 기존 제품(50㎛이상)보다 월등히 가늘어 가볍고 통기성이 우수하며 내열성·통전성·내식성이 탁월하다고 덧붙였다.
특히 석면을 전혀 방출하지 않는 친환경 소재로 인체 유해성 논란이 일고 있는 저가의 폴리에스테르나 유리섬유 소재를 대체할 수 있을 것으로 기대했다. 이번 기술개발과 관련해 2건 국내외 특허등록을 마친 연구팀은 오는 4월부터 알팩을 통해 양산에 들어갈 예정이다.
박부근 알팩 사장은 “일본이 선점한 알루미늄섬유 부직포 제조기술보다 향상된 기술을 국산화한 것”이라며 “향후 대학 연구진과 함께 구리·스테인리스강 등을 이용한 금속섬유 부직포 제조기술 개발에 연구역량을 집중하겠다”고 밝혔다.
이정환기자@전자신문, victolee@