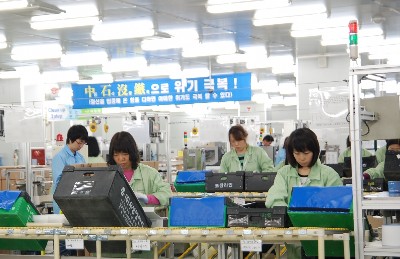
경기도 평택 LG전자 디지털 파크. 지난 13일 찾은 디지털 파크 ‘G2’ 공장은 물류 차량으로 북새통을 이뤘다. G2는 LG전자의 휴대폰 글로벌 생산거점 중 하나다. 전 세계에 팔리는 LG 휴대폰 가운데 절반가량을 이곳에서 생산하고 있다. 생산 규모만 얼추 연간 5000만대에 달한다. 불과 두 달 전만 해도 한산했던 G2 공장에 ‘대형 사고’가 터졌다. 생산라인이 완전 가동 체제로 돌아섰다.
경기 불황으로 공장 밖은 여전히 한겨울인데 정작 공장 안은 화창한 봄이었다. ‘생산라인 풀가동’. 믿기지 않지만 사실이다. ‘불황 무풍지대’가 따로 없었다. 이상철 단말 제조그룹 부장은 “미국 수출 물량이 터지면서 공장 가동률이 95%를 웃돌고 있다”고 말했다. 지난해 11월부터 생산량이 줄기 시작해 1월 초 가동률이 60% 안팎까지 떨어졌다. 그러나 1월 말부터 회복하기 시작해 지금은 거의 쉬는 라인이 없다. 2교대 20시간에 일부 라인은 잔업까지 이어지고 있다. LG전자 측은 “아레나폰·쿠키폰 같은 프리미엄폰이 미국· 유럽에서 반응이 좋기 때문”이라며 “생산 가동 현황만 보면 미국 시장이 회복기로 접어들었다고 착각할 정도”라고 말했다.
LG전자 ‘G2’ 공장에 전 세계 휴대폰 생산 물량이 몰리는 데는 철저한 생산공정 혁신의 결과다. G2 공장은 초기만 해도 노키아 등 경쟁업체를 벤치마킹해 생산라인을 구축했다. 그러나 지금은 휴대폰 디자인뿐 아니라 생산 방식에도 LG만의 고유 색깔을 입히는 데 성공했다. LG전자는 먼저 다른 층에도 별개로 운영하던 자재와 부품 창고를 생산라인 옆으로 모두 이동했다. ‘자재·생산라인 일관 시스템’을 구축한 것이다. 생산 현장에서 바로 자재와 부품 수량 파악이 가능해져 그만큼 낭비 요소를 줄였다. 실시간으로 부품 재고를 관리하는 동시에 생산 시간도 크게 단축했다.
생산라인의 핵심인 시험·검사공정도 대대적으로 손질했다. 휴대폰 라인은 세탁기·냉장고와 같은 가전과 달리 검사 공정이 전체 생산라인의 80% 가량을 차지한다. 모든 부품을 모듈 형태로 위탁 업체에서 가공해 줘 케이스·배터리를 포함해 10개 안팎의 부품을 조립하면 그만이다. 대신에 라인 대부분에는 하드웨어 내구성에서 소프트웨어·통화·무선강도·사업자ID 설정까지 복잡한 검사 시험 장비가 빼곡히 들어차 있다.
LG는 휴대폰 모델에 따라 검사장비를 교체하지 않고 손쉽게 바꿀 수 있는 ‘팰릿 시스템’으로 공정을 전면 개선했다. 이상철 부장은 “팰릿 방식은 전 세계 휴대폰 공정 중 유일하게 LG가 개발한 방식”이라며 “이 방식을 도입하기 전에는 모델에 따라 검사장비를 바꾸는 데 2∼3일이 걸렸지만 지금은 평균 15분, 단순 플랫폼은 5분 이내에 바로 교체할 수 있다”고 말했다. 이 때문에 G2 공장에서는 별도의 라인 교체 없이 30개 라인에서 무려 300개의 모델을 일괄 생산한다. 그만큼 유연한 생산 시스템을 확보한 것이다.
마지막으로 품질 혁신이다. G2 공장은 휴대폰 조립 라인이지만 설계 당시부터 반도체 클린룸 수준의 청정도를 확보했다. 이 때문에 불량률이 휴대폰 업계의 최고 수준인 ‘100PPM’ 경지에 올라 섰다. 100만대 가운데 100개, 1만대 중에 1대 정도가 문제 있을 정도로 생산성을 크게 높여 놓았다. LG전자 측은 “G2 생산 공정을 중국·브라질·인도 등 다른 공장에서 바로 활용할 수 있도록 글로벌 스탠더드화하는 데 주력하고 있다”고 말했다.
강병준기자 bjkang@etnews.co.kr