![[스마트빅뱅] 똑똑해진 포스코 제철소 현장](https://img.etnews.com/photonews/1105/136992_20110527132532_607_0001.jpg)
“50초마다 쇳덩이 제품이 하나씩 흘러나오는데 이 쇳덩어리 하나가 2000만~2500만원짜리입니다. 하지만 설비가 삐끗해 흠이 생기기 시작하면 뒤따라 나오는 모든 제품에 흠이 생겨 쓸 수 없을 지경이 됩니다.”
포스코의 제철공장 관리를 위한 가장 중요한 업무는 수많은 설비가 ‘똑바로’ 가동되고 있는지 일일이 확인하는 일이다.
땀 맺힌 얼굴로 넓은 공장을 두루 다니며 손수 장비를 점검하는 현장의 작업자들. 이들은 필요로 하는 것을 하나씩 만들어 나가자며 ‘똑똑한 공장 만들기’ 프로젝트를 시작했고, 불과 1년 사이 제철소의 모습은 완전히 바뀌었다.
◇RFID와 스마트폰이 만난 ‘꿈의 공장’=이형진 포스코 설비기술부 팀장은 “예전에는 프린터로 점검 시트를 출력해 나열된 항목을 눈으로 체크하면서 장비를 점검했고, 사무실에 돌아와 시스템에 다시 결과를 입력했다”며 “하지만 이제는 설비에 부착된 전자태그(RFID)를 스마트폰으로 인식시키면 점검해야 할 항목이 폰 화면에 뜨고, 폰 화면에 점검결과를 입력하면 3G망을 탄 정보가 곧장 서버로 간다”고 설명했다. 이 공장에만 3000여 현장 작업자들의 스마트폰에서 RFID 정보를 읽을 수 있는 드라이버가 장착돼 있다.
오랜 경험을 녹여 포스코ICT가 직접 개발한 ‘크래들’은 중계기 역할을 한다. 점검하고자 하는 장비 근처에 가면 이 크래들이 RFID의 태그 정보를 받아 ‘어떤 장비’인지, ‘무엇을 점검해야 하는지’ 등을 스마트폰으로 전송해준다. 이 크래들은 설비의 온도까지 측정해낸다.
스마트폰에 탑재된 설비관리솔루션은 설비점검 리스트 등을 보여줌은 물론이고 설비 이상 발생 시 현장에서 스마트폰으로 촬영한 사진과 영상을 전문가와 실시간 공유할 수 있는 기능까지 갖췄다. 예전에는 점검자가 사무실에 돌아와 문제를 확인한 후 다시 사람을 내보내 조치를 해야만 했다.
장비가 있는 그 자리에 한번 가서 점검부터 결과 입력, 비상조치까지 끝낼 수 있게 된 것이다. 이 공장에선 이를 ‘현장완결형’이라고 명명했다. 이 팀장은 “이 기술 도입 이후 점검에 소요되는 시간만 30%가 단축됐고, 점검에서 누락되는 설비도 없어지면서 점검 실행력은 99%로 향상됐다”고 말했다. 반드시 장비에 가까이 가서 체크를 해야 하니 점검자가 딴청(?)을 피울 수도 없게 됐다. 점검의 오류와 정확도가 높아졌음은 물론이다.
◇알아서 위험관리까지 ‘척척’=포스코는 이 같은 설비점검관리를 포함해 안전방재, 자재관리, 운송관리 등 크게 4가지 영역의 스마트 제조공장 프로젝트를 지난해 본격적으로 추진했다. SK텔레콤과 협업해 제조공장 전체에 3G 인프라를 구축하고 통신 사각지대도 없앴다.
시스템 구축을 지휘한 오창식 포스코ICT 스마트워크 팀장은 “작업 지시와 점검 실적을 관리하는 데이터베이스관리시스템(DBMS)을 스마트폰에 탑재했다”며 “음영지역에서 나오는 순간 자동으로 정보를 동기화하고 서버와 연계되도록 했다”고 설명했다.
이 제철소 공장 안의 모든 위험 시설물에도 RFID가 부착돼 있다. 만약 작업자들이 근처에 가서 RFID 정보를 확인하면 이 위험 시설물에 대한 체크 리스트가 뜬다. 가스 설비 등 위험기구 시설확인부터 ‘리스크 TOP10’ 점검이력·상태점검 및 평가, 가동 중 설비 출입감시까지 한다. 이어 올 연말까지 GPS 기술도 접목된다. 작업자가 위험물 근처에 가면 GPS를 통해 자동으로 접근에 대한 경고신호를 줘 이전에 일어난 사고 이력까지 알려주도록 할 계획이다. 추가적으로 CCTV까지 스마트폰으로 모니터링할 수 있는 기능을 개발 중이다.
◇자재관리부터 공장 내 운송계획까지=공장 창고에 가면 수급되는 자재에도 RFID가 부착돼 있다. 자재 입하검수, 반납 등 업무 처리를 모두 크래들과 스마트폰으로 실시간 할 수 있다. 기존에는 재고 실사에만 보름에서 한 달 정도의 시간이 소요됐지만 이젠 하루이틀이면 충분하다는 것이 작업자들의 감탄 섞인 설명이다.
올 초에는 공장 내 ‘운송차량’도 한층 똑똑해졌다. 차량의 위치를 추적하고 최적의 스케줄을 짜주는 운송차량관제솔루션 덕택이다. 공장 밖 어디에 있더라도 GPS를 이용해 운송차량의 위치를 파악하고, 이를 중앙에서 통제해 운송지시를 내린다. 가장 짧게 이동하면서 가장 많은 짐을 나를 수 있도록 한다. 빈 차로 넓은 공장을 배회하지 않아도 돼 유류비와 시간을 아낄 수 있다.
각 차량의 운전자들은 자신의 스마트폰으로 자신이 실어 날라야 할 짐의 위치 정보를 알 수 있다. 이 같은 노력으로 공차 비율은 48%로 줄었다. 오 팀장은 “공장 내 운송차량에 내비게이션을 탑재하고 SK텔레콤과 함께 공장 내부를 그린 특수 지도를 만들었다”며 “제철소 밖에 나가면 이 지도가 자동으로 시스템에서 안 보이도록 했다”고 말했다. 보안 때문이다.
포스코의 제철소 공장은 지금 이 순간에도 진화하고 있다. 연말까지 전 범위에 걸친 고도화 프로젝트를 진행 중이며, 내년 이후 변화할 새로운 공장의 모습도 기대가 된다.
유효정기자 hjyou@etnews.co.kr
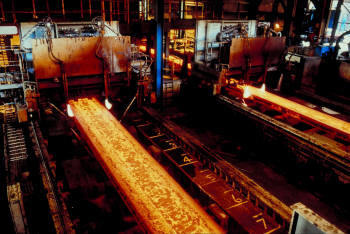
![[스마트빅뱅] 똑똑해진 포스코 제철소 현장](https://img.etnews.com/photonews/1105/136992_20110527132532_607_0003.jpg)
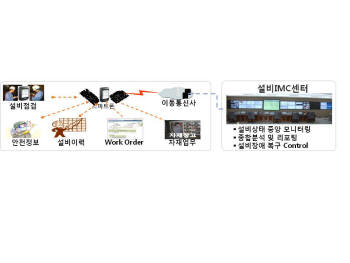
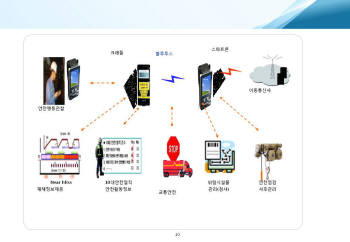