독일 산업이 에너지와 정보통신기술(ICT)을 중심으로 재단장하고 있다. 지능형 공장을 앞당기는 ‘인더스트리 4.0’ 기조에 맞춰 생산성을 높이고 에너지 효율을 극대화했다.
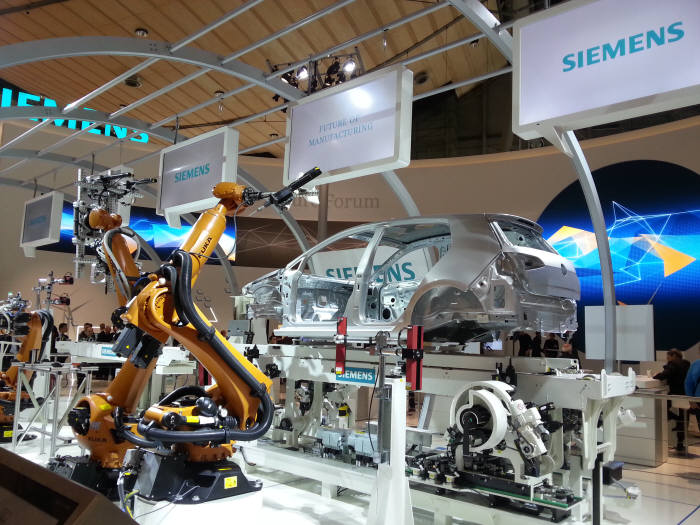
지능형 공장은 제품 생산 전 과정 최적화를 추구해 불필요한 움직임이나 시간 낭비를 최소화 한다. 사물인터넷(IoT) 기술을 적용해 제품, 보관소, 생산설비 등 생산과정에 있는 모든 개체를 식별하고 여기서 모아진 데이터를 분석해 최적화된 생산 활동을 수행하는 것이다. 지능형 공장을 100% 실현하지 못하더라도 부분적인 산업자동화도 에너지 비용 등 지출을 줄일 수 있다.
지능형 공장에서는 시뮬레이션과 최적화로 에너지 효율을 높인다. 생산설비 에너지소비를 24% 줄일 수 있다. 생산 라인에서 에너지 소비를 모델링, 시뮬레이션, 시각화, 최적화해 적용한다. 이를 통해 제품·재료 흐름과 에너지 관련 특성에 대한 결합·분석이 가능해 에너지 소비를 줄이는 전략을 짤 수 있다. 폴크스바겐 공장과 프라운호퍼 연구소 등 독일 곳곳에 이 기술이 적용됐다.
지능형 공장에 적용된 대표 기술로 ‘에너지 복구 기능을 갖춘 주파수 변환기’가 있다. 이 기술을 적용하면 제동으로 인한 속도 저하 현상이 빈번히 발생하는 승강기, 원심 분리기 또는 컨베이어 벨트 등에 필요한 에너지 소비를 줄일 수 있다. 생성된 제동 에너지를 전력으로 변환해 사용할 수 있어 승강기 등 설비에서 소모하는 에너지를 최대 50%까지 절약한다. 하이브리드 자동차에 연비 향상을 위해 적용한 회생 제동 기술을 공장에서 사용하는 것이다.
로베르트 노이하우저 지멘스 모션제어시스템사업부 사장은 지능형 공장을 구축했을 때 최대 장점으로 ‘제품 생산시간 단축과 에너지비용 절감’을 꼽았다. 공장의 모든 데이터가 한 곳으로 모여 최적화된 생산 활동을 수행하기 때문에 제품 생산 시간이 줄어든다. 또 공장의 전력피크 관리에도 효과적이라는 설명이다.
지능형 공장에서는 생산설비가 스스로 에너지소비량을 진단하고 연결된 다른 설비와 커뮤니케이션하면서 에너지 효율이 폭발적으로 높아진다. 공장 에너지 수요는 피크타임과 평상시로 나뉘는데 에너지 공급은 생산설비에 문제가 발생하지 않도록 항상 피크에 맞춰져 낭비가 발생한다.
하지만 지능형 공장에서는 생산설비가 서로 규약(우선순위)을 맺어 행동한다. 공장에서 가장 큰 설비가 가동되는 타이밍에 다른 설비가 돌아가지 않는 것이다. 여러 생산설비가 동시에 에너지를 소비하지 않도록 관리, 과거에는 최고 100의 전력이 필요했던 공장이 80의 전력으로도 제품을 생산할 수 있다. 노이하우저 사장은 “지능형 공장이 되면 생산설비 간 커뮤니케이션을 통해 무궁무진한 에너지 절약이 가능하다”며 “사물인터넷을 적용한 생산 설비 사이에 간단한 규약을 만드는 것뿐이지만, 공장에서 얻는 에너지절감 효과는 크다”고 말했다.
하노버(독일)=
함봉균기자 hbkone@etnews.com