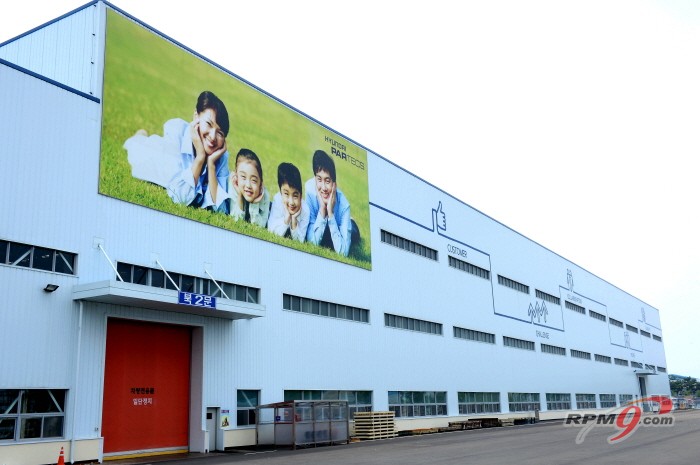
무엇이든 오래 사용하는 습관을 가진 사람이라면 `단종된 제품`이란 말에 한번쯤은 눈물을 훔친 경험이 있을 것이다. 정든 제품을 더 이상 사용할 수 없게 되기 때문. 만약 그게 자동차라면 더 큰 문제다. 새 제품을 사는 데 큰 비용이 들 뿐 아니라, 고장을 방치하면 안전에도 큰 문제를 불러올 수 있다. 이에 단산차종을 책임지는 업체가 있다. 바로 현대파텍스 얘기다.
지난 17일, 충남 서산에 위치한 현대파텍스를 찾았다. 현대파텍스는 이미 단종된 차의 패널 부품을 전문적으로 만드는 업체다. 지난 2005년 현대자동차와 기아자동차, 현대모비스가 초기 자본금 400억원의 56%, 31%, 13%를 각각 분담해 설립했다. 20만7,316㎡(6만2,713평) 부지에 건물 면적 6만9,157㎡(2만920평) 규모로 이뤄졌으며, 프레스라인과 자동 생산이 가능한 로봇 등 다양한 설비도 갖췄다.
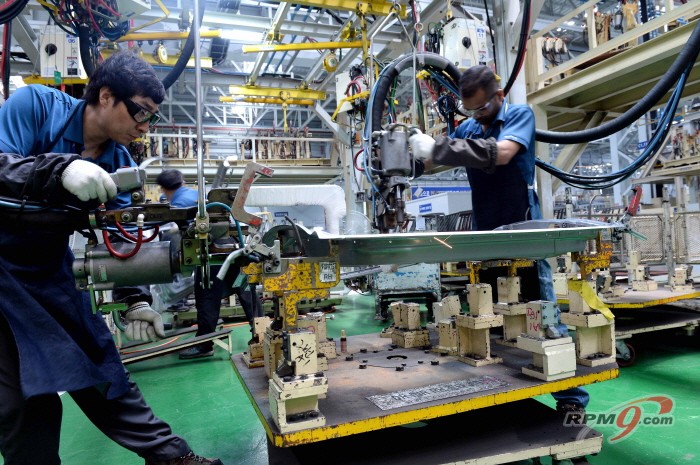
파텍스는 현대와 기아자동차에서 단산된 차종 금형을 들여와 보관하고, 주문이 들어오면 생산하는 방식으로 사업을 진행한다. 현대차 2,902개, 기아차 1,936개 등 4,800여 개에 달하는 금형틀을 보유하고 있으며, 1세대 그랜저까지도 생산할 수 있다. 올해는 아반떼 HD와 제네시스 BH 금형을 들여왔다. 단산 차종에 대한 서비스를 지속적으로 제공할 수 있고, 설비에 중복으로 투자하는 것도 막을 수 있어 회사 입장에서는 1석 2조인 셈이다.
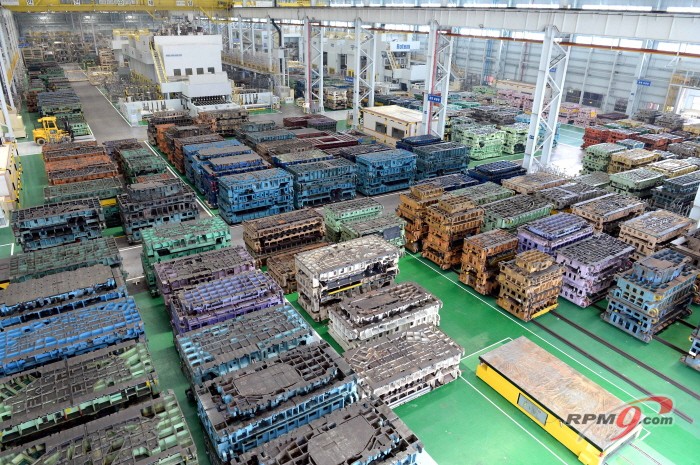
생산현장은 프레스라인과 차체조립라인, 도·포장라인 등으로 구성됐다. 먼저, 9,915평 규모의 프레스라인은 연 440만 샷(Shot)에 달하는 생산 능력을 갖추고 있다. 문, 후드, 무빙류와 프런트 펜더 등을 다루며, 로봇을 이용해 자동으로 생산한다. 이날 현장에서는 `1,200톤`, `800톤`, `500톤`으로 이어진 프레스 라인이 베르나에 들어가는 부품을 만들고 있었다. 각 수치는 샷을 내리칠 때 발휘하는 가장 큰 힘을 의미한다. 각 공정 사이에 위치한 로봇이 작업을 마친 부품을 옆 공정으로 옮겨줬다.
차체조립라인은 연 100만개 부품을 생산할 수 있으며, 헤밍프레스 8기, 로봇 27대로 운영한다. 주로 생산하는 부품은 무빙류 7종과 프런트 펜더 등이다. 지그와 금형을 교체해 다양한 차종 생산에 대응할 수 있고, 품질 관리를 위해 기계와 사람이 이중으로 점검하기도 한다.
마지막으로 도·포장라인에서는 앞선 두 공정이 마무리된 제품에 색을 입히고, 포장하는 과정이 이뤄진다. 330m 길이의 이 설비에선 도장, 전처리, 전착, 건조, 언로딩, 포장 순으로 공정이 진행된다. 전처리 과정에서 이물질을 제거하고 약품처리를 하며, 전착 과정에선 제품을 22㎛(약 0.022mm) 두께로 얇게 도장한다. 아울러 160℃ 이상에서 20분 정도 건조하면 도장 과정이 끝나며, 내수와 수출용으로 분류해 제품을 포장한다.
파텍스는 제품 제작 외에 금형과 제품 관리에도 신경을 기울이고 있다. 야외에 보관하는 약 3,300개 금형은 이물질로부터 보호하기 위해 비닐로 포장해 뒀으며, 생산에 필요한 경우 세척과 점검 과정을 거쳐 적합한지 여부를 검토한다. 이를 통해 손상된 부분이 발견됐을 경우 보수작업을 진행한다. 또 완성된 제품은 형태와 크기에 맞게 제작된 전용 팔레트에 보관한다. 향후엔 비슷한 제품끼리 공유할 수 있는 통합 팔레트를 마련해 보관에 있어서도 효율을 높이겠다는 방침이다.
이 회사 관계자는 "파텍스가 프레스, 차체, 도장, 포장에 이르는 모든 작업을 일괄적으로 진행하기 때문에 시간을 단축할 수 있고, 다차종 소량 생산 노하우가 축적돼 있어 부품을 보다 안정적으로 공급할 수 있다"고 말했다. 아울러 "노후화된 금형을 이용해 좋은 품질의 제품을 내놓기 위해 품질관리와 제품 보관 방법 등을 회사 차원에서 늘 고민하고 있다"고 덧붙였다.
서산(충남)=
차재서기자 jscha@etnews.com