일반 공작기계에 ICT를 적용한 ‘똑똑한’ 기계 제작 기술이 처음 개발됐다.
한국기계연구원(원장 임용택)은 김동훈 초정밀시스템연구실 책임연구원 연구팀이 ‘무인 가공공정 최적화 및 지능화 기술개발 사업’의 일환으로 일반 공작기계에 내장(Builtin) 센서를 이용해 가공 정밀도를 실시간 제어할 수 있는 시스템을 개발했다고 29일 밝혔다.
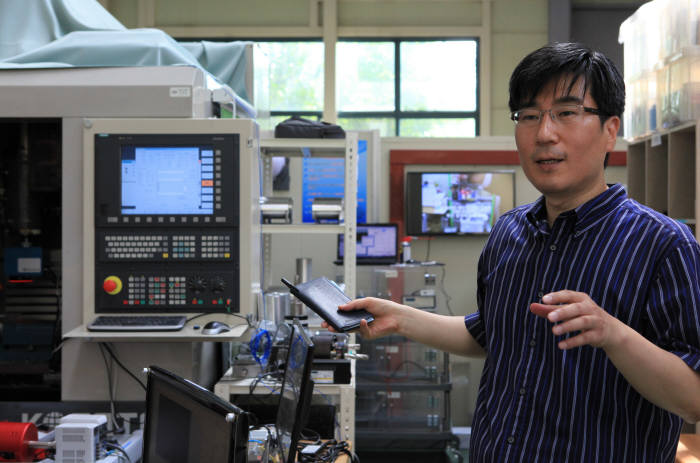
이 시스템은 자율화 및 지능화 기능을 동시에 제공해 기존의 생산 효율을 획기적으로 향상시킬 수 있다.
연구팀은 무인 가공공정을 최적화하기 위해 가공물의 가로, 세로 크기뿐만 아니라 두께를 자율인식 하는 기능을 탑재했다. 또 열·진동으로 인한 변형을 동적으로 예측·보정할 수 있는 수치제어기(CNC)를 지능화시켰다.
역진동을 이용해 진동으로 인한 기계 떨림도 대폭 억제시켰다.
공구에 탈·부착식 센서를 달아 무선(블루투스)으로 공구의 절삭력을 감지함으로써 적정 시점에 공구를 교환할 수 있도록 했다.
연구팀은 이를 통해 실시간 가공정밀도는 50%, 생산 효율은 30% 이상 증가시켰다고 설명했다.
기존에는 가공물의 크기 및 두께를 사람이 직접 파악해 기계의 초기 가공원점을 사전에 설정해야 했다. 기계를 장시간 가동할 때 열과 진동이 발생해 가공의 정밀도가 저하된다는 점도 문제였다. 계절이나 시간에 따른 열 발생 정도도 다르고 작업 중 발생하는 공구의 회전속도에 따른 변형도 발생했다.
김동훈 책임연구원은 “생산제조장비 IT 융합 및 지능화 분야의 국내 시장규모는 현재 약 3조9000억원으로 연평균 9.5% 성장하는 블루오션 영역”이라며 “향후 자동차, 조선, 항공 등 여러 분야에서 생산 효율성을 높이는 데 크게 기여할 것”이라고 말했다.
한편 이 기술은 2014년도 국가연구개발우수성과 100선에서 기계·소재 분야 우수성과에 선정됐다.
대전=박희범기자 hbpark@etnews.com