산업용 3D프린팅 기술이 해외 제조업 현장에서 목업(Mockup)과 시제품 제작을 넘어 양산 공정으로 적용 분야를 확대하고 있다. 양산 공정을 완전히 대체하지는 못했지만 절삭(밀링), 주조(캐스팅), 사출성형 등 기존 공법과 융합해 생산성과 부품 성능을 높이고 있다.
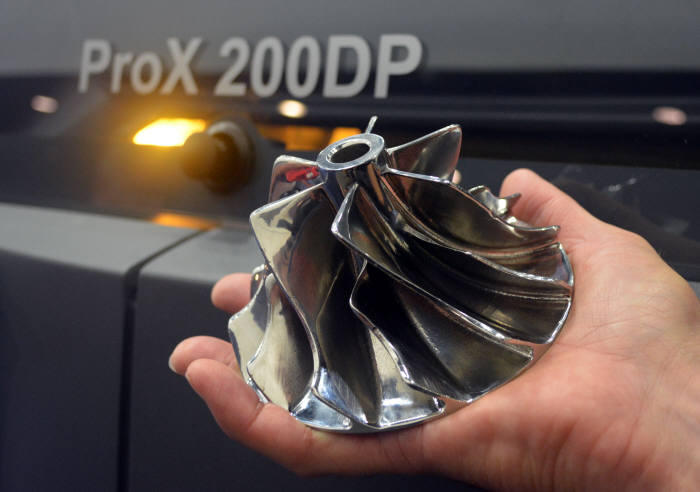
프랑스 타이어 제조업체 미쉐린은 3D프린터 20여대를 타이어 표면의 홈 무늬(트레드 패턴) 성형용 몰드 제작에 사용하고 있다. 트레드 패턴은 미세한 변화에 따라 차량 구동과 제동, 선회 성능, 승차감, 소음 등 타이어 성능에 영향을 주는 핵심 요소다.
기존 밀링 방식으로는 복잡한 패턴을 정확하게 형성하기 어려웠지만 3D프린팅 기술로 몰드 제작 시간을 대폭 줄였다. 성능 개선을 위한 패턴 변화를 빠르게 양산 제품에 적용할 수 있고 오류 수정과 불량률 감소에도 기여했다.
항공 산업에서는 3D프린터가 부품 양산에 직접 사용된다. 보잉과 제너럴일렉트릭(GE), 하니웰, 록히드마틴, 에어버스 등 글로벌 업체는 대부분 금속 소재와 플라스틱 소재 등 부품별로 3D프린팅 기술 적용 분야를 분류해 범위를 늘려가고 있다.
고부가가치 정밀 제품을 다품종 소량 생산하는 만큼 양산 효율성을 다소 떨어지더라도 복잡한 형상을 정확하게 만들 수 있는 3D프린팅이 성능 향상에 유리하기 때문이다. 기존 공법으로는 8개 부품을 따로 만들어 조립해야 했던 부품을 일체형으로 만들 수 있고 부품 내부를 3차원 구조로 설계해 무게를 줄이면서 강도를 높일 수 있다.
보잉은 2만2000여종 군용기와 여객기용 항공 부품을 3D프린터로 만들어 공급할 계획이다. 플라스틱 소재로 구성된 인테리어 내장재와 에어덕트부터 메탈 프린터로 직접 가공하는 제트엔진용 블레이드, 연료 노즐 등이다.
GE도 별도 연구센터를 설립, 2020년까지 10만종 제트엔진 관련 부품을 생산할 방침이며 중국 항공·우주비행연구소는 길이 12미터에 달하는 3D프린터로 에어버스, 보잉 등과 경쟁할 비행기용 부품 제작을 연구하고 있다.
스위스 명품 시계브랜드인 롤렉스와 같은 소비재 산업에서도 메탈 3D프린터를 디자인과 성능, 조립성 검증 테스트용 시제품과 양산용 금형 제작에 이용하고 있다. 미국은 국가 3D프린팅 연구 기관 NAMI(National Additive Manufacturing Innovation Institute)를 중심으로 중소 금형·주조 업체 3D프린팅 적용 사례가 늘고 있다.
백소령 3D프린팅시스템즈코리아 3D프린터사업부장은 “미국은 물론이고 중국에서도 제품 양산 공정에 3D프린팅을 응용해 품질과 성능을 향상시키는데 공을 들이고 있다”며 “기존 공정을 그대로 사용하되 품질과 불량률을 낮추고 금형 개발과 제작기간, 제품 개발주기 단축 등을 위해 산업용 3D프린터가 접목되는 것”이라고 말했다.
박정은기자 jepark@etnews.com