국내 연구진이 금속 3D프린팅으로 서로 다른 금속을 적층해 소재 강도는 높이면서 제작비용은 낮추는 금형 제작 공법을 개발했다. 금형을 활용하는 다양한 뿌리산업에 적용해 생산 수율을 높이는 데 기여할 것으로 기대된다.
한국생산기술연구원(원장 이성일)은 성지현 대경지역본부 극한제조기술그룹 박사팀이 '직접금속툴링(DMT) 3D 금속 프린팅' 기술을 활용해 고기능·저비용의 이종소재 금형을 만들 수 있는 공법 기술을 개발했다고 3일 밝혔다.
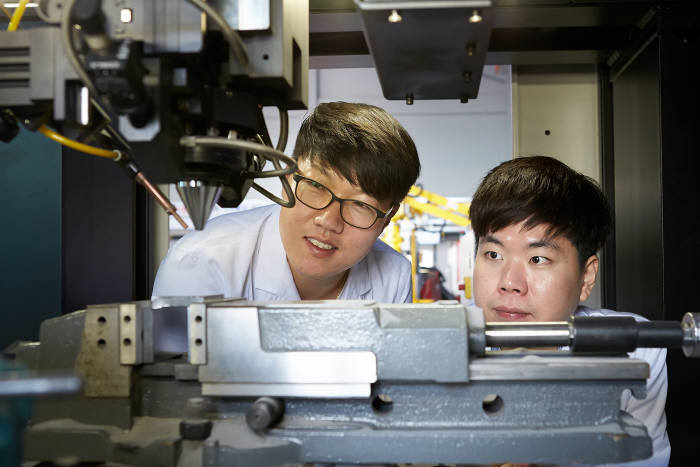
DMT 3D 금속 프린팅 기술은 고출력 레이저 빔으로 금속 표면에 '용융풀'을 만들고, 이를 접함점으로 삼아 다른 금속 파우더를 적층하는 기술이다. 성질이 다른 두 금속을 단단하게 접합시킬 수 있다.
이 기술은 금속 강판을 자르는 '전단 금형' 분야에 적용할 수 있다. 자동차와 항공기에 고강도 강판 사용이 늘고 있으나 고강도 금속만 사용해 금형을 만들면 제작비용이 높아진다.
이번에 개발한 DMT 3D 금속 프린팅을 활용한 이종소재 금형 제작 공정은 저렴한 일반 금속 소재로 전단 금형을 만들고, 강판을 자르는 부위에는 고강도 금속을 적층하는 방식이라 제작비용을 대폭 낮출 수 있다.
연구팀은 앞으로 '고강도 특수금형강(M2)' 소재 적층법을 개발해 기가 파스칼(㎬·강도 단위) 수준의 고강도 강판을 자를 수 있는 금형을 만들 계획이다. 이종소재 금형에 활용할 수 있는 금속 물질을 확보해 데이터베이스화하는 작업도 병행할 예정이다.
우선 '핫스탬핑' 금형 개선에 도전했다. 핫스탬핑은 950도 이상 온도에서 강판을 성형한 후 급속 냉각시켜 강도를 높이는 과정이다. 열전도율이 높은 금형을 만드는 것이 관건이다. 연구팀은 핫스탬핑 금형 표면에 열전도도가 높은 스텔라이트(코발트를 주성분으로 한 합금) 금속을 적층해 고기능성을 확보했다.
이종소재 금형 기술은 파손 금형 보수, 리모델링에도 활용된다. 파손 부위에 다른 금속을 덧대거나 오래 전에 쓰던 금형을 새롭게 바꾸는 것도 가능하다.
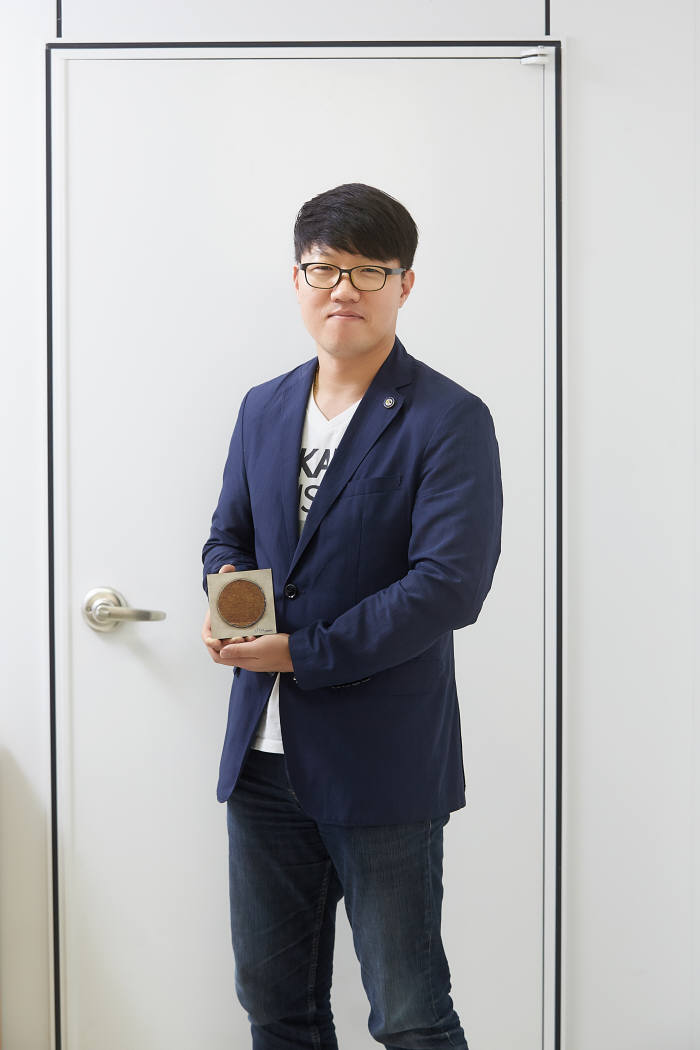
성지현 박사는 “서로 다른 성질의 금속을 3D프린팅으로 적층해 새로운 금형을 만드는 공법 기술을 개발했다”면서 “이 공법을 국내 금형산업에 적용하면 뿌리산업 전반에서 큰 발전을 이끌 수 있을 것”이라고 말했다.
대전=김영준기자 kyj85@etnews.com