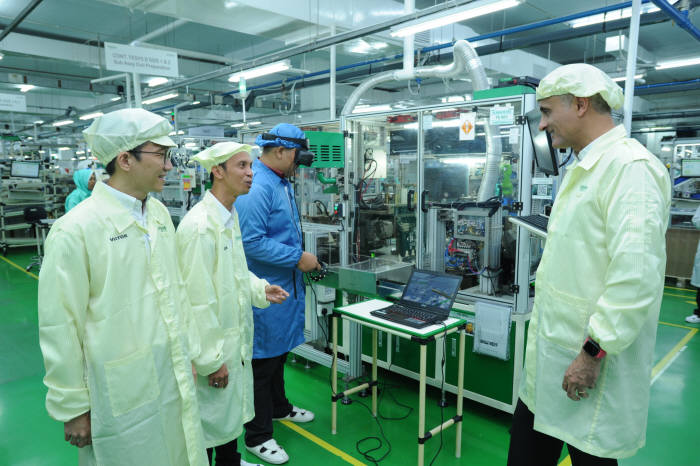
#인도네시아 정부는 슈나이더일렉트릭 바탐 스마트공장을 '4차 산업혁명 등대공장(제조업 미래를 밝혀주는 현장)'으로 대표 지정했다. 슈나이더일렉트릭은 개방형 통합 아키텍처 플랫폼인 에코스트럭처를 적용, 삭막한 공장을 정보통신기술(ICT)과 융합해 세계 최고 수준 스마트공장으로 탈바꿈시켰다. 2017년 전(全) 공정 디지털 전환에 성공, 에너지 효율과 직원 생산성을 각각 7%, 17% 이상 개선하는 효과를 창출했다.
지난 25일 기자가 찾은 인도네시아 바탐 스마트공장에서는 방진복을 착용한 직원들이 전자개폐기(컨택터)를 생산하고 있었다. 일반 공장과는 달리 대부분 근로자가 VR기기·스마트글래스를 착용하거나 태블릿으로 무언가를 열심히 체크하는 모습이 눈에 띄었다. 공정마다 최첨단 ICT를 접목해 생산 효율성을 극대화하는 과정이 돋보였다.
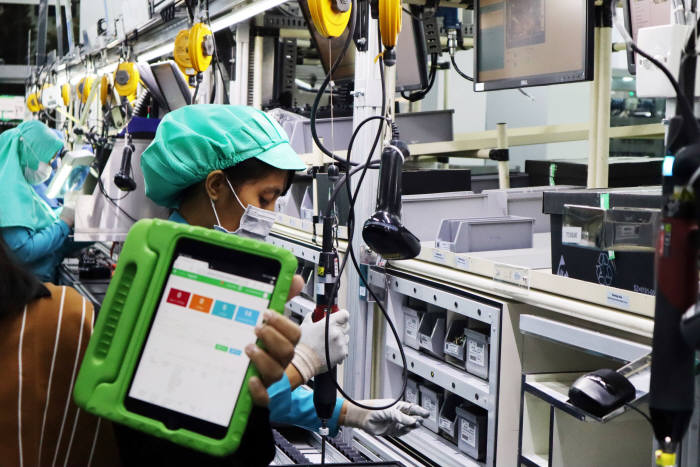
VR기기를 착용한 직원은 고개를 이리저리 흔들며 대만에서 전송한 신제품 디자인을 꼼꼼히 체크하고 있었다. 기존에는 신제품 디자인을 확인하기 위해 다른 국가 주문자상표부착생산(OEM) 업체에 방문했는데 바탐 스마트공장에서는 타국에서 보내온 제품 디자인을 3차원(3D) VR로 꼼꼼히 체크하며 이동시간·비용을 절약했다.
또 다른 직원은 기기 문제를 해결하기 위해 중국에 있는 전문가와 '스마트글라스'로 의견을 주고받으며 해결 방법을 찾느라 여념이 없었다. 해외 전문가가 원격으로 공장 기기 문제를 같이 살펴보며 피드백을 제공하는 모습은 참신했다.
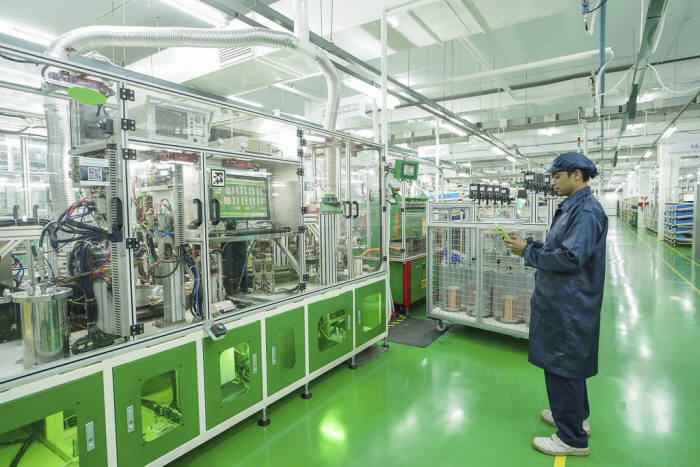
증강현실(AR) 태블릿은 스마트공장 '안전지키미' 역할을 톡톡히 했다. 직원이 태블릿 카메라로 공장 기기를 담으면, 기기에 대한 상세정보가 화면에 나타났다. 가령 A기기 두번째 서랍을 비추면 비상작동버튼이 있다는 메시지가 뜨고, 비상버튼에 문제가 생겼을 땐 빨간 경고등이 깜빡거리며 근로자에게 현황을 전달하는 식이었다. 야근을 하거나 신입직원 근무 중 문제가 발생하더라도 차분히 대응할 수 있다는 점을 실감했다. 빠르게 작동하는 기기에 손을 대지 않고 핵심 정보 및 문제점을 파악할 수 있어 안전성이 확보된다는 장점이 뚜렷했다.
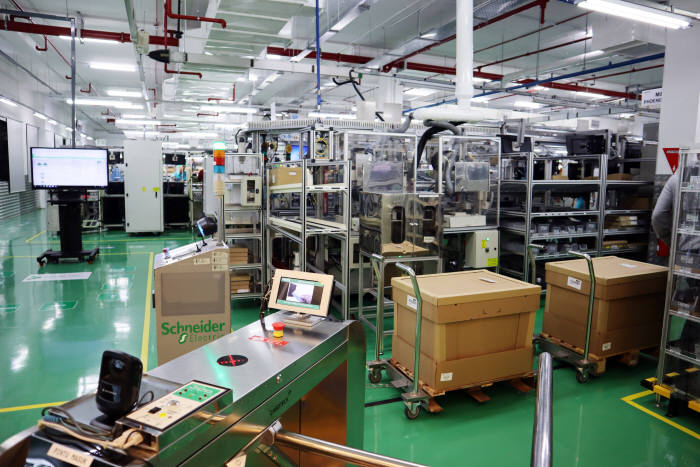
운반 로봇(AGV)은 마치 화물을 적재한 기차가 레일 위를 달리듯, 포장된 컨택터 상자를 지정 장소로 옮기느라 분주했다. 작업자는 구간별로 설치된 모니터에서 공정 이상 유무를 확인, 인공지능(AI) 기술이 기기 온도까지 체크하며 만일사태에 철저히 대비하고 있었다. 직원이 실수로 불량품을 다음 공정으로 넘기더라도 기기가 자동으로 걸러내는 것은 물론, 관리자가 외부에서 스마트폰으로 공장 가동현황을 실시간 파악하는 건 이곳에선 낯설지 않은 모습이었다.
공장 한편에 마련된 '디지털 트레이닝룸'은 신입 직원이 실제 공장과 비슷한 ICT 환경에서 교육을 받는 공간이다. 오른쪽 팔꿈치에 완장을 찬 트레이너는 신입 직원에게 VR기기·스마트글래스·태블릿 등 사용법은 물론 어떤 효과를 기대할 수 있는지도 설명했다. 트레이닝 과정을 빨리 통과하려는 신입 직원 열정은 인도네시아에 내리쬐는 햇볕만큼 뜨겁게 느껴졌다.
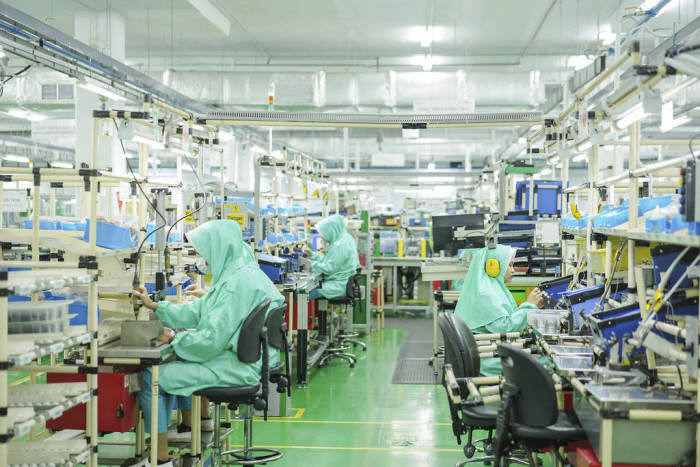
스마트공장 투어를 마치고 나가려던 찰나에 '숏 인터벌 미팅'이라고 적힌 공간이 눈길을 사로잡았다. 각 공정별 대표 직원이 옹기종기 모여 15분간 △생산 공정은 원활했는지 △문제는 없었는지 △비상상황에 적절히 대응했는지 등 의견을 공유했다.
'스마트공장은 기계가 사람을 대신하는 것이 아닌, 사람이 하는 일을 기계가 스마트하게 보조하는 역할'이라는 현장 직원들의 신념을 확고히 느낄 수 있는 순간이었다.
바탐(인도네시아)=
최재필기자 jpchoi@etnews.com