BMW가 올해 하반기 국내 출시하는 'iX'는 BMW 브랜드 최초의 스포츠액티비티차량(SAV)이자, 세 번째 배터리 전기차(BEV)다. BMW는 iX에 강력한 차제 구조를 핵심 무기로 삼았다.
전기차 에너지 효율을 높이기 위해 무게를 최대한 줄이면서, 차체 강성과 충돌 안전성을 높이기 위해 각 부품들이 요구 사항을 정확하게 만족시킬 수 있도록 엄선된 소재와 제조 공정 기술을 적용했다.
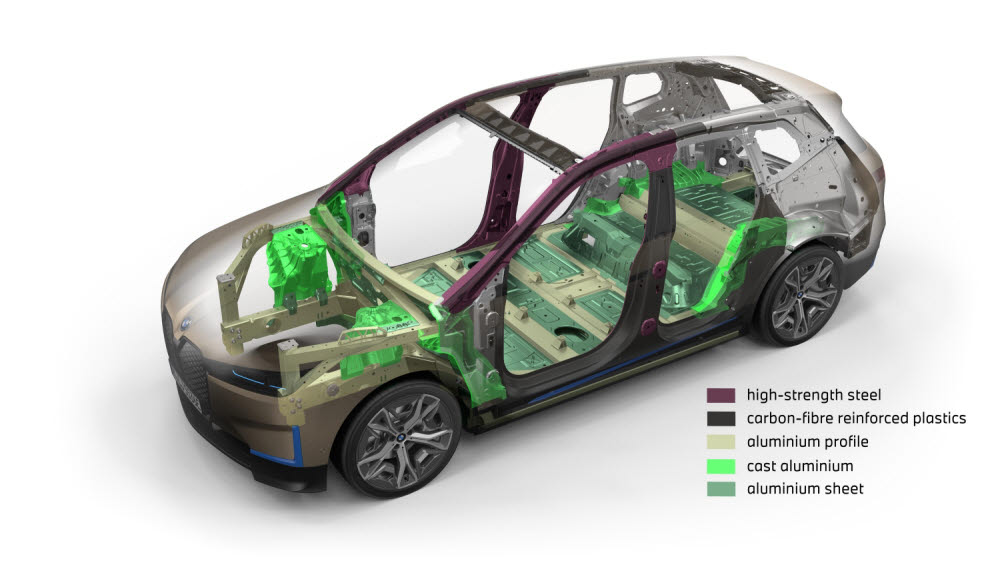
BMW iX는 동급 최초로 알루미늄 스페이스 프레임 구조뿐만 아니라, 최첨단 차체 쉘(차체 중 도어·보닛·트렁크 등을 제외한 부분)에는 탄소섬유강화플라스틱(CFRP)과 고성능 열가소성 수지, 고강도 강철, 알루미늄 등이 사용됐다.
BMW iX의 차체의 사이드·루프 프레임, 카울 패널(전면 윈도와 연결된 앞쪽 부분), 리어 윈도우 프레임은 탄소섬유강화플라스틱으로 제작돼 '카본 케이지(Carbon Cage)'를 형성한다.
카본 케이지는 7시리즈에 사용된 카본 코어에서 진화한 차체 구조로, 탑승공간의 안전성을 강화시킨 설계로 무게 밸런싱 등의 최적화를 통해 민첩한 주행성능을 지원한다.
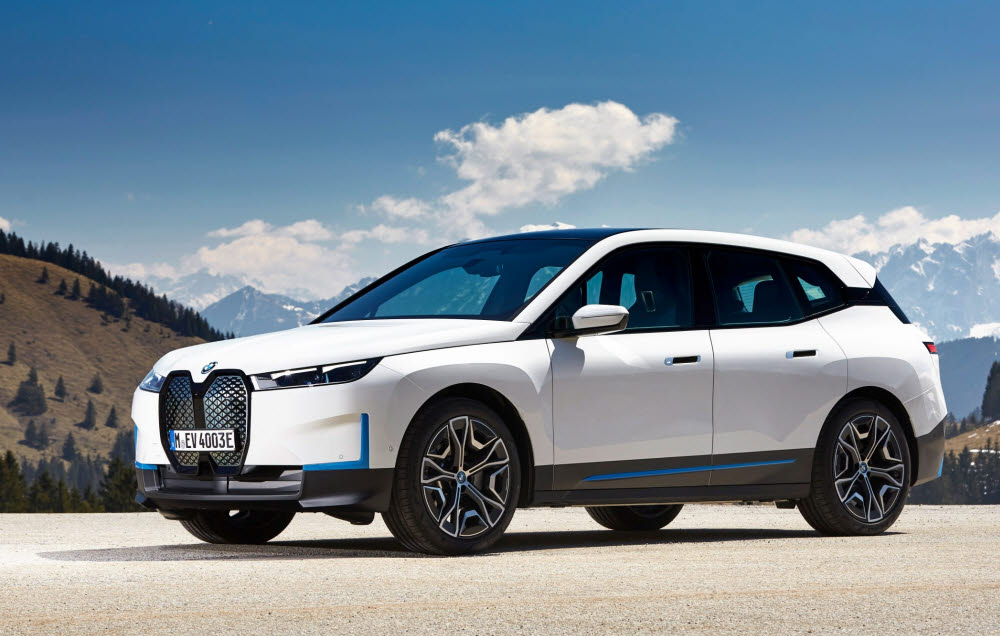
사이드 프레임과 리어 엔드에 사용된 탄소섬유강화플라스틱은 BMW iX에 시각적 차별화 포인트로 주목된다. 카본 소재만의 특징은 좌우 도어와 트렁크가 열렸을 때 분명한 존재감을 드러낸다. 이는 iX의 하이테크적인 이미지와 함께 탄소섬유의 다층 배열이 제공하는 입체감까지 느낄 수 있다.
카울 패널 및 리어 윈도우 프레임의 구성 요소는 완전히 새로운 공법이 적용된 '연속 섬유강화 열가소성 수지(CFRTP)'로 제작된다. CFRP와 CFRTP 등은 특히 효과적인 경량 설계 수단으로 활용된다. 혁신적 소재 조합은 아주 슬림한 형태의 기초를 형성해 실내 공간감을 더하며, 제어장치나 세척액 라인, 배선 하네스용 브라킷을 부품에 통합해 제작할 수도 있다.
iX에 적용된 CFRTP구조는 강성을 증가시키면서 강철로 만든 유사부품에 비해 약 5kg 경량화했다는 것이 BMW 설명이다.
BMW그룹은 BMW i 모델과 BMW 뉴 7시리즈 생산 경험에서 축적된 하이테크 경량 소재 관련 노하우와 CFRP 적용으로 차체 무게를 획기적으로 줄였다. BMW그룹은 지난 10년 간의 재료 및 공정 기술 개발로, 탄소섬유 차체 부품의 품질과 생산성 향상을 통한 경쟁성까지 확보했다는 설명이다.
CFRP는 충격 등으로 인한 안전성을 유지하면서도 차체 제작에 사용되는 재료 중에 가장 가벼운 소재다. 탄소섬유는 보기 드문 인열 저항성 덕분에 섬유의 특징을 지니면서도 높은 수준의 강도를 자랑한다. 특히 이 같은 특징들은 주어진 하중에 따라 최적화도 가능하다.
동물 뼈나 식물 줄기와 같이 자연 생물들이 각자 필요한 부분에는 두껍고 강한 구조를 지닌 것과 같은 이치다. BMW는 하중이 예상되는 방향으로 필요한 만큼의 섬유를 정렬시킨 구조로 제작됐다. 이 때문에 관련 부품들은 필요조건에 따라 그 강성을 유지하면서도 경량화에도 유리하다.
CFRP 생산은 전구체 섬유를 통해 추출되는 소재기술도 포함된다. 이 전구체 섬유는 양털로 만들어진 직물에서도 찾아볼 수 있는 폴리아크릴로니트릴(PAN)으로 구성된다.
다양한 온도나 압력 조건에서 수행되는 여러 과정을 통해 섬유 내 다양한 구성요소들이 하나씩 차례로 가스화되고, 이후 약 7 미크론(μm) 남짓 되는 두께의 섬유만이 남게 되는데, 이 섬유는 안정화된 흑연 구조를 가진 100% 탄소로 구성된다. 0.007mm 두께의 이 섬유 직경은 사람 모발의 직경 10분의 1에 수준으로 얇기 때문에 약 5만개의 필라멘트를 모아 조방사(Ovings) 또는 묵직한 토우(화학섬유의 굵은 타래)로 뭉쳐 적용하게 되는 구조다.
박태준기자 gaius@etnews.com