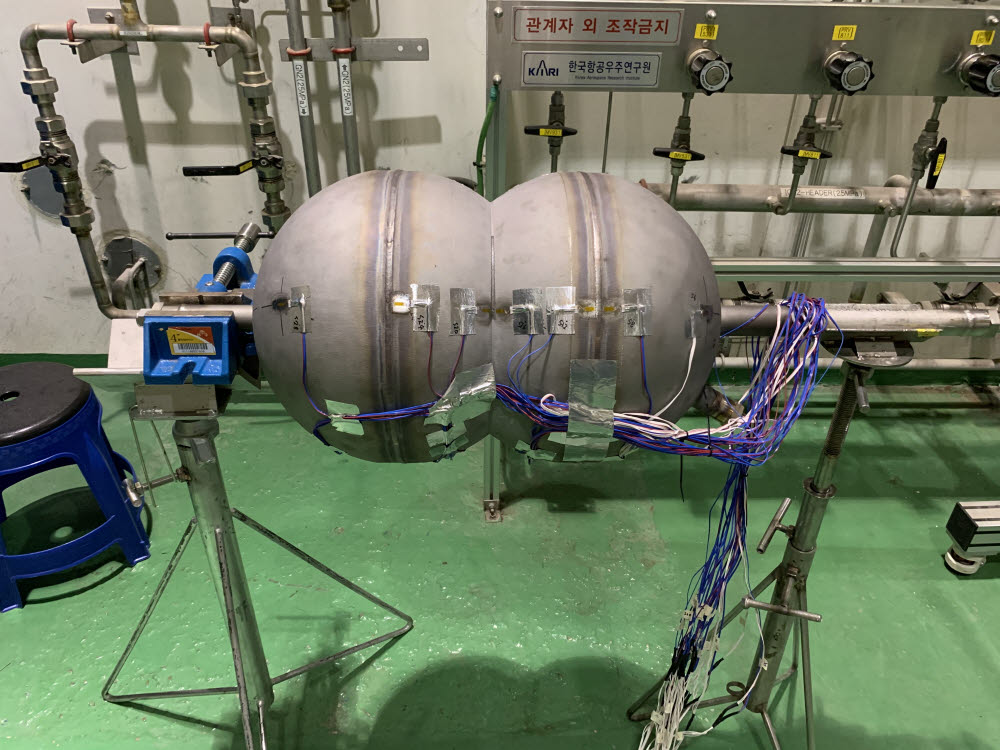
한국생산기술연구원(원장 이낙규)은 손용 3D프린팅제조혁신센터 연구원팀이 금속 3D프린팅 기술로 우주 발사체용 추진제 탱크 시제품 제작에 성공했다고 24일 밝혔다.
이 시제품은 한국항공우주연구원(원장 이상률) 미래발사체연구단 성능평가에도 합격, 상용화 기대감을 높였다. 양 기관은 지난해 10월 '항공우주부품 제조자립 업무협약'을 체결, 이번 성과 창출에 나섰다.
개발 시제품은 금속 3D프린팅 기술을 적용해 두 개 탱크를 한데 합친 공통격벽(두 개 구형이 위아래로 겹쳐진 형상) 형태다.
기존 발사체용 추진제 탱크는 '산화제'와 '연료' 탱크를 별도로 제작, 이어붙인 형태다. 숫자 '8'과 같다. 이 경우 불필요한 여백이 생기고 부피도 커 공간 효율성이 떨어졌다.
손 박사 연구팀은 탱크 벽면 위에 또 다른 탱크를 바로 겹쳐 쌓아 올리는 제작 기법을 고안했다. 이는 소형발사체 상단 설계 시 공간 효율성을 12% 높이고, 부품무게는 27% 낮춘다.
연구팀은 복잡한 형상 구현을 위해 직접 에너지 적층(DED)방식 금속 3D프린팅 기술을 적용했다. DED방식은 공정 시간이 길어질 경우 열 누적으로 제작품 열변형을 일으킬 수 있어, 기존에는 주로 소요시간이 짧은 파손 부품 보수 등에만 쓰였다. 이번에는 실시간 공정 모니터링을 더해 공정 변수를 적절히 제어, 제작시간이 긴 추진제 탱크 부품도 고품질로 제작하는데 성공해다.
공통격벽 구조 축소 추진제 탱크는 30bar 내압 성능평가에서 합격점을 받았다.
생기원은 향후 3D프린팅 기술이 성형, 용접 및 절삭 등의 전통적 우주발사체 탱크 생산방식을 대체하고, 구조 설계의 자유도 향상, 공정 자동화, 제작 기간 단축 등의 효과를 이끌어 낼 것으로 기대했다.
손용 연구원은 “해외에서는 이미 다품종 소량생산의 맞춤형 항공우주부품 제작에 3D프린팅 기술이 적극적으로 활용되고 있다”며 “항우연과 협력해 3D프린팅 기술 적용 항공우주 부품 개발과 제조산업 혁신을 앞당길 것”이라고 밝혔다.
대전=김영준기자 kyj85@etnews.com