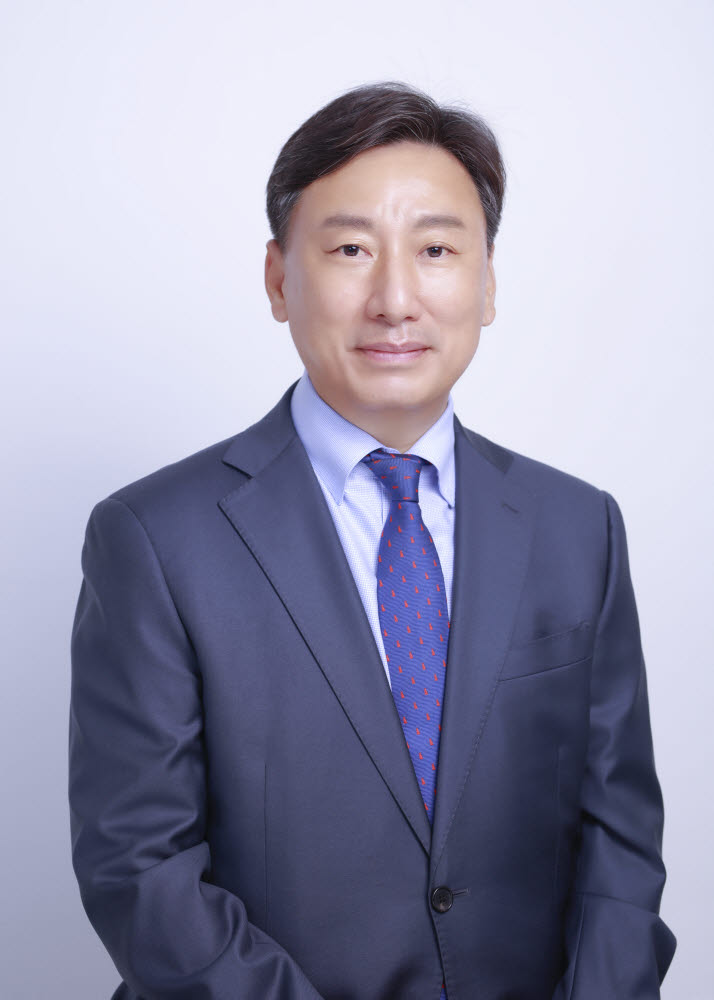
스마트팩토리 전환 과정에서 제조 현장 '데이터'는 중요한 요소다. 이에 제조 장치, 설비 등에 센서를 부착해 작업 정보나 데이터를 취득하고 결과 값에 대응하고 있지만 인력 작업에서 데이터를 취득하기란 녹록지 않다.
사람에 의한 작업은 원래 센싱이 어렵다. 계측용 디바이스를 장착하면 이는 곧 작업자의 부담이 돼 장치 사용 누락으로 데이터 정확도가 떨어진다. 실제 인력 작업 데이터 취득에 대해선 아직 정답이 보이지 않는 상황이다.
이병석 한국페트라이트 지사장은 “인력 작업 가시화로 스마트팩토리 성과를 만들어 가는 공장이 있다”며 그 성공 사례를 제시했다. 신호 정보기기 글로벌 선두기업 페트라이트가 일본 효고현에서 직접 운영하는 산다(SANDA) 공장이다. 산다 공장은 무선 데이터 통신 시스템 'WD PRO'를 제조 현장에 적용해 가동률 현황을 실시간 파악해 비 작업 시간을 대폭 감소하는데 성공했다.
그는 “한국의 경우 스마트 팩토리 도입과 전문가 고용에 대한 비용부담으로 스마트 팩토리 구축에 어려움을 겪는 중소기업이 많다”면서 “간단, 신속, 경제적인 WD PRO 시리즈는 한국 중소기업에 스마트 팩토리 실현을 앞당기는 대안이 될 것”이라고 설명했다.
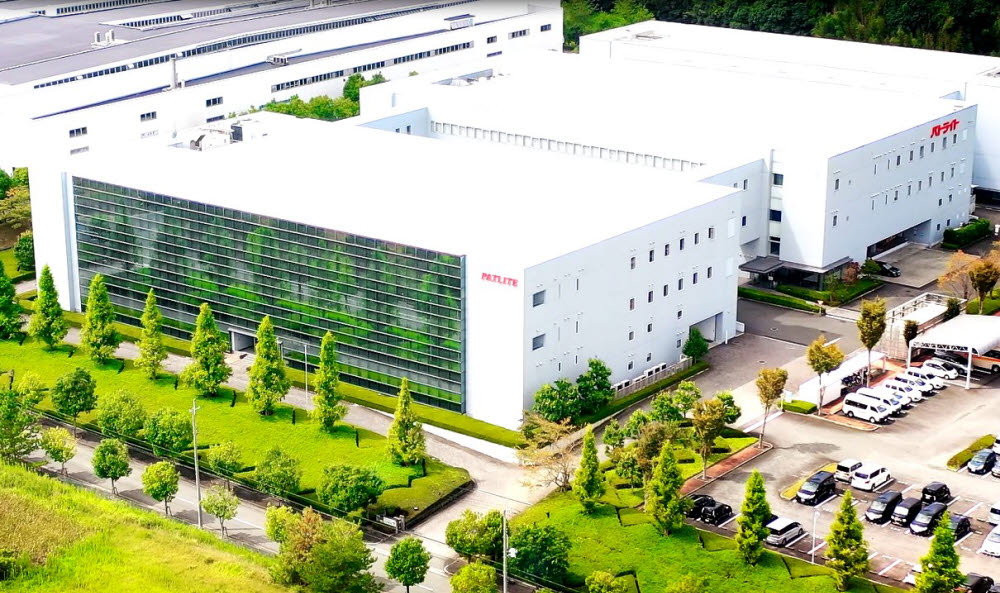
-일본 효고현 산다 공장 역할은.
▲산다 공장은 산업용 신호기기 제조 공장 중심 역할을 맡고 있다. 신제품은 주로 산다 공장에서 생산한다. 설계 개발 부문과 함께 생산 설계 등을 검증하거나 샘플 라인에서 시제품부터 제품 양산까지 다양한 검증을 진행한다. 산다 공장 양산 공정은 인도네시아 공장으로 이전한다.
양산품은 인도네시아 공장에서 생산하기 때문에 산다 공장은 기본적으로는 수주 생산에 대한 다품종 소량 생산을 담당한다. 또 싱글·플렉시블 '셀(본인 완결형 생산방식)' 등으로 구분해 생산량, 진척도 등에 맞춰 대응한다.
-무선 데이터 통신 시스템 'WD PRO'를 도입한 배경은.
▲생산성 개선을 위해 WD PRO를 도입했다. 공장 설비 시그널타워에 추가 설치하는 것만으로 설비 가동 상황을 파악할 수 있다. 설비 가동 상황을 보여주는 경광등 정보를 보면 최소한 가동 상황은 모을 수 있다.
스마트 팩토리 관심이 높아지면서, 간단한 설비 가시화가 가능해 인기를 끌었지만 산다 공장에선 처음 사내 도입을 생각하지 않았다. 당초 이 제품은 설비에 사용하는 것으로 인력 작업이 중심인 산다 공장에는 도입이 어렵다고 판단했다.
그런데, WD PRO를 사내에서 설비 감시 이외 다른 용도로 사용할 수 없느냐는 목소리가 나왔다. 그래서 '다품종 소량 생산'으로 고민하던 산다 공장에서 제품을 도입해 인력 조립 생산에서 실제 사용할 수 있는지를 확인해 보자는 움직임이 생겨났다.
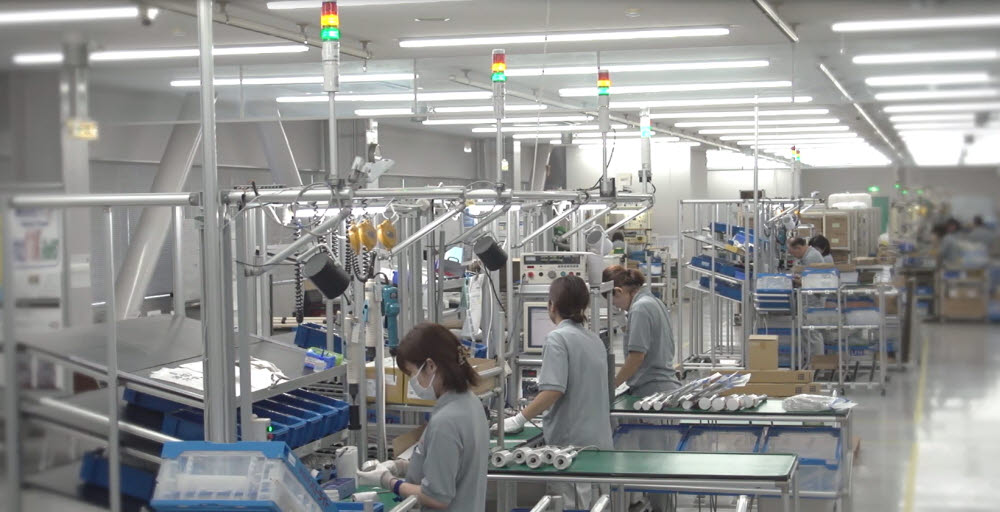
-산다 공장 조립 생산 과정에 초기 도입해 실패한 이유는.
▲데이터를 너무 상세하게 취합하다 보니 작업자 부담이 컸다. 다품종 소량 생산이란 특성상 교체시간이 길어질 수밖에 없다. 우선 작업 상태가 어떤 상황인지 파악하고자 작업대에 스위치 박스를 설치해 '단계설정' '작업 중' 등 스테이터스 버튼을 누르는 프로세스를 생각했다. 결과적으로 이 방식은 성공하지 못했다.
작업자는 손으로 입력하는 과정에서 잘못 누르거나 잊어버리는 일이 발생했다. 이런 일이 빈번하게 일어나면 데이터 정확도를 신뢰할 수 없다. 그래서 2017년 말 작업자에게 추가 업무 부하를 주지 않고 센서 등을 활용해 작업 상황을 취합해 데이터화하는 방향으로 바꿨다.
- 근로자 비 작업 시간을 대폭 축소한 배경은.
▲처음엔 1개 생산 라인에만 설치해 조립, 검사, 포장 등 세 가지 공정을 진행하는데, 실제 데이터를 취득해 보니 비 작업 시간이 15.6%나 존재했다. 그 내용을 분석하면, 조립 공정에선 부품을 가져오는데 손실이 컸다. 또 검사 공정과 포장 공정은 이동하는 범위가 넓어져 결과적으로 근로자가 작업 구역에 없는 시간이 많다는 것을 파악했다. 이런 데이터 분석을 통해 로스 상황을 파악해 실제로 개선 활동을 추진했다.
조립 공정에서 개선 활동을 시작한 후 전용 공급 대차를 만들고, 작업자가 작업 구역을 떠나지 않고 작업을 계속하는 환경을 만들었다. 또 검사 공정과 포장 공정의 '이동' 문제는 사용 설비를 한곳에 집약해 작업 구역을 떠나지 않고 작업을 했다. 이 같은 노력으로 3개월 만에 비 작업 시간을 15.6%에서 8.3%로 줄였다.
안수민기자 smahn@etnews.com