무게를 철의 4분의 1 수준으로 줄이면서도 강도는 10배 높일 수 있는 탄소섬유 복합소재 제조 기술이 개발됐다. 배터리를 비롯한 전장부품의 중량이 증가하는 수소·전기차 차체 경량화를 위한 핵심 기술로 기대된다.
한국생산기술연구원(원장 이성일)은 윤길상 뿌리산업기술연구소 금형기술그룹 박사팀이 차량 루프로 쓸 수 있는 탄소섬유 복합소재 고속 금형·성형 기술을 개발했다고 20일 밝혔다.
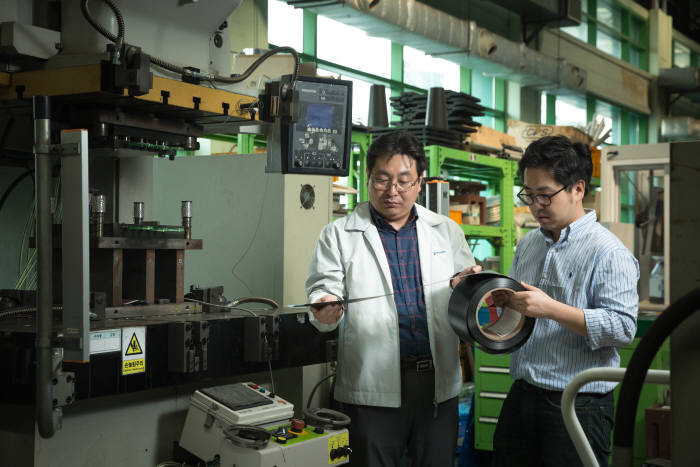
탄소섬유 복합소재는 무게가 철의 4분의 1 수준이지만 강도는 10배인 차세대 소재다. 미래 자동차의 새로운 차체 소재로 주목받고 있다.
자동차 활용에는 아직 제한된다. 설계 성능을 유지하면서 짧은 시간 안에 생산하기 어려워 대량 생산이 안 됐다. 범퍼와 같이 다소 작은 크기의 부품에만 활용해 왔다.
연구팀은 1.3×1.7m 크기의 차량 루프를 7분 만에 금형·성형하는 공정 기술을 개발했다. 이런 대면적 부품의 10분 안 고속 생산은 자동차 선진국인 미국이나 독일에서도 구현하지 못한 기술이다.
이 기술의 핵심은 탄소섬유 복합소재를 짧은 시간에 굳히는 것이다. 연구팀은 자체 개발한 '신속경화제'로 경화 시간을 대폭 줄였다. 외국 기업이 주로 쓰는 열가소성수지(CFRTP) 대신 열경화성수지(CFRP)를 이용했다. CFRP는 높은 온도에서 분자가 서로 결합, 별도의 경면 처리 공정 없이도 광택을 낸다.
연구팀은 정밀 온도제어로 불량품을 없앴다. 미리 열을 가한 금형으로 소재를 압축하는 공정을 이용, 금형 부분별 온도 편차를 정밀 계산해서 최적화된 열 공정을 구현했다.
생기원은 이 공정 기술을 조만간 상용화할 방침이다. 2019년께 완성차 생산 공정에 반영할 수 있도록 할 계획이다.
윤길상 박사는 “크기는 커졌지만 반대로 제조 시간은 줄어든 탄소섬유 복합소재 금형·성형 기술을 개발했다”면서 “루프는 자동차 부품 가운데 가장 큰 부품으로, 얼마든지 다른 부품에도 공정을 적용할 수 있다”고 설명했다.
대전=김영준기자 kyj85@etnews.com