한국항공우주연구원(원장 임철호)이 발사체 제작비용을 크게 낮출 수 있는 기반기술 확보에 나섰다. 3차원 적층(3D 프린팅) 기술을 활용해 발사체 핵심 구성품을 저렴하고, 빠르게 제작하는 방식이다. 발사비용을 낮추는 것이 중요한 소형발사체 기술 확보에 기여할 전망이다.
임병직·이금오 선임연구원 등 항우연 미래발사체연구단 연구진은 3D 프린팅 기반 발사체 부품 제작 기술을 개발하고 있다고 18일 밝혔다. 이 기술을 활용하면 발사체 '키 컴퍼넌트' 역할을 하는 요소들을 기존 방식보다 훨씬 저렴하게 제작할 수 있다.
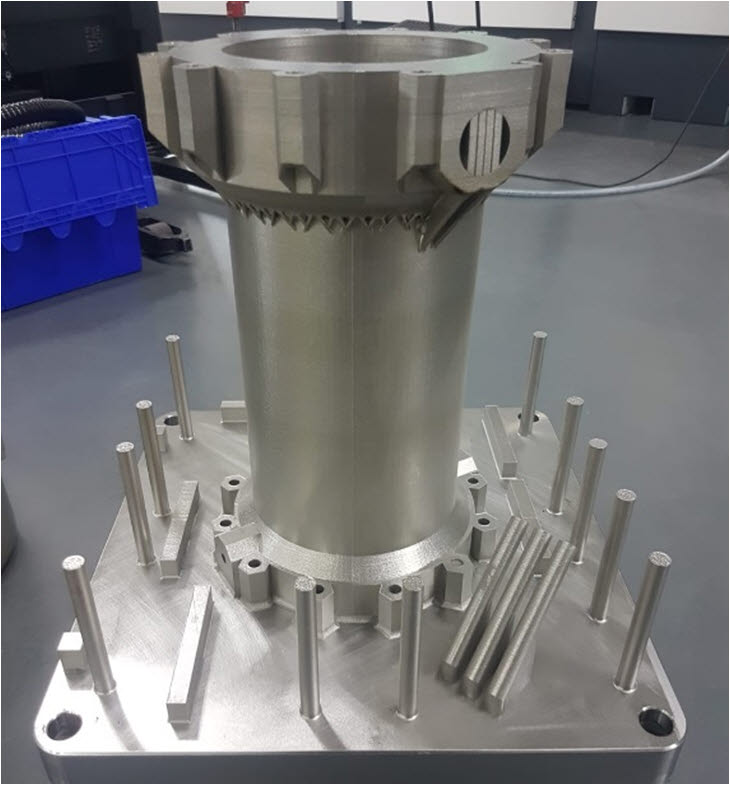
대표 연구 분야는 복잡한 구조를 갖고 있는 엔진 헤드 부분이다. 한국형발사체 누리호에 쓰이는 75톤 엔진은 헤드에 총 700개 분사기(인젝터)가 들어간다. 분사기 자체도 3개 구성품으로 이뤄진다. 전통적 방법으로는 각 요소를 일일이 만들어 시험하고, 조립·결합하는 복잡한 과정을 거쳐야 한다. 제작비용이 천정부지로 치솟는다.
반면에 3D 프린팅 기술을 활용하면 인젝터를 담은 상태로 한 번에 헤드를 구성할 수 있다. 이 분야에서 연구진은 이미 성과를 내고 있다. 3D 프린팅을 적용, 여러 절차를 해소한 결과 제작비용을 5분의 1 이하로 줄일 수 있게 됐다. 또 기존에는 어려웠던 헤드 형태, 분사기 내부유로 방향 조절도 가능하게 했다.
기술 검증도 마친 상태다. 실제 연소시험을 거치지는 않았지만 2톤급 엔진 규모에서는 물과 공기를 이용해 설계 특성을 확인했다. 연구진은 향후 헤드뿐만 아니라 엔진 실린더와 노즐, 추진제 탱크 등에도 기술을 적용할 계획이다.
이 기술은 중대형발사체에도 활용할 수 있지만 미래발사체연구단이 선행연구 중인 소형발사체에 더 효과적으로 활용할 수 있다. 3D 프린팅 기술 적용이 본격화 돼 제작비용을 낮추면 발사비용을 크게 낮출 수 있다. 비용이 중요한 소형발사체 개발에 청신호가 켜진 셈이다. 미래발사체연구단은 오는 2025년으로 예정된 소형발사체 체계 사업 전에 관련 기술을 확보할 계획이다.
이기주 항우연 미래발사체연구단 소형발사체 담당은 “3D 프린팅으로 발사체 제작단가를 크게 낮추는 기술은 현재 세계에서도 일부만 활용하는 혁신 기술”이라며 “현재 주요 기술은 어느 정도 확보한 상태이며, 곧 실제 적용도 가능해질 것”이라고 말했다.
대전=김영준기자 kyj85@etnews.com