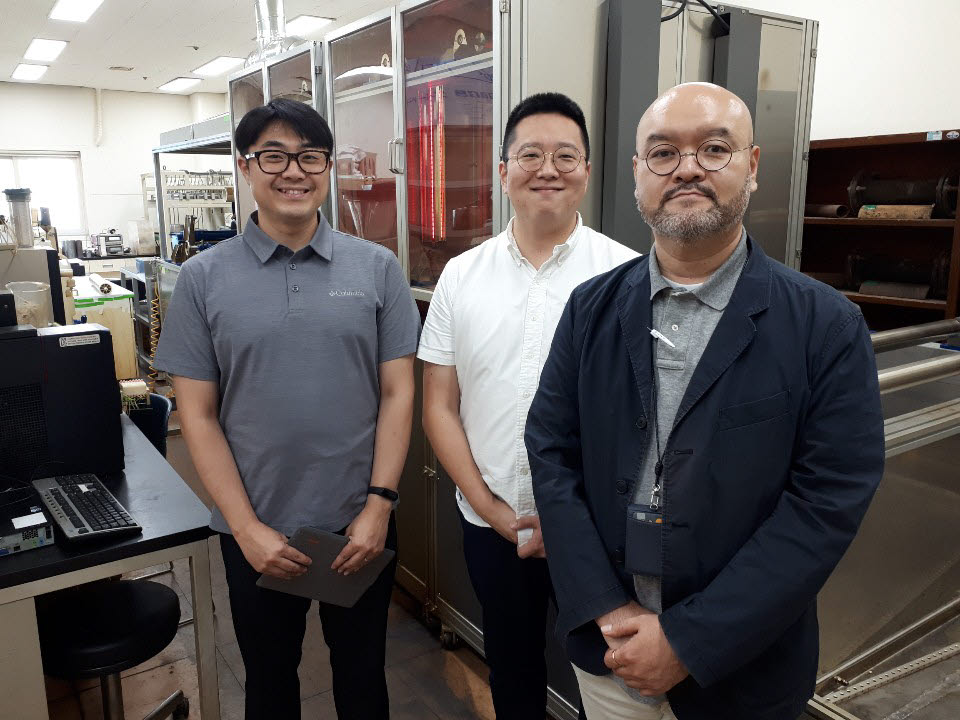
한국건설기술연구원 국토환경실험동 210호 환경실험실. 다양한 해수담수화 기술 성과가 움트는 곳이다.
문을 열고 들어서면 공간을 가득 채운 크고 작은 설비가 눈에 들어온다. 큰 것은 높이가 사람 키를 넘어서고, 길이는 키 두 배를 넘는 듯 보인다.
연구실을 책임지는 최준석 연구위원은 이들 설비를 활용해 두께가 밀리미터(㎜) 수준인 얇은 막, '멤브레인'을 만들어낸다고 설명했다.
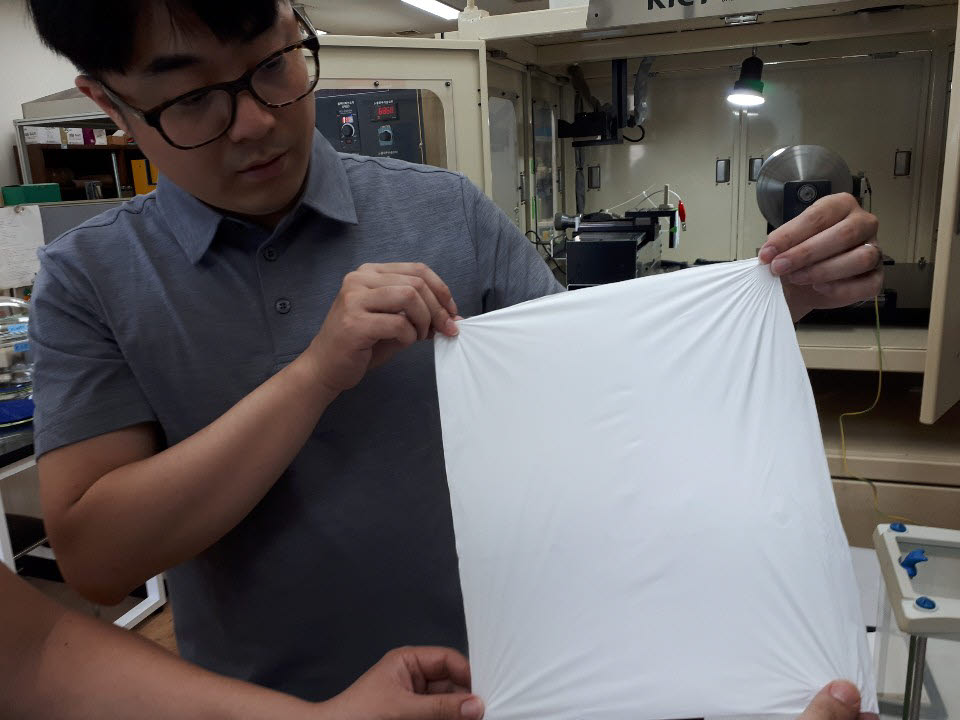
설명에 따르면 멤브레인은 해수담수화에 핵심 역할을 하는 요소다. 공극을 통해 물은 통과시키면서 다른 요소는 걸러내는 것이 기본적인 활용법이다. 고기능 멤브레인을 구현, 에너지를 덜 소모해 담수화를 이루는 것이 과제다.
최 위원은 “폴리머(고분자)로 멤브레인을 만드는데, 어떤 첨가제를 쓰고 어떤 조건을 구현하느냐에 따라 성질이 달라진다”며 “정답이 없어 수많은 시행착오로 원하는 물성을 찾아낸다”고 말했다.
설명에 이어 실제 멤브레인 제작과정을 볼 수 있었다. 박광덕 연구원이 연구실 한 켠의 '특수 막 전기방사장치'로 막을 제조하는 과정을 보여줬다.
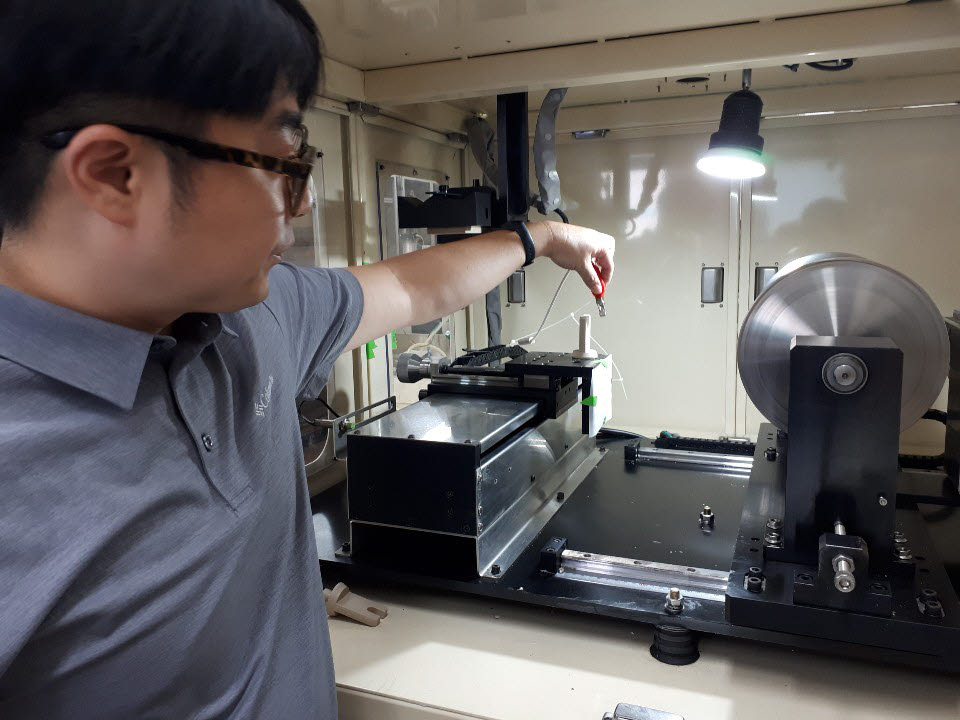
방사한 폴리머가 회전하는 원통에 달라붙기를 반복, 면을 이루는 방식이다. 신기해하는 기자에게 박 연구원이 '전하를 가한 결과'라고 설명했다. 주사기에 양극 전극을 연결하고 원통 뒤에는 음극 전극을 연결, 전류 이동을 따라 폴리머가 움직이게 했다는 설명이다.
A4 용지 크기를 만들려면 4~5시간이 걸린다고 했다. 하루에 많이 해도 3장을 만들기가 어려운 시간이다. 연구팀은 이 과정을 셀 수 없이 반복해 원하는 물성의 멤브레인을 만들어냈다.
뒤이어 대형 제막 장비를 접했다. 이 장비는 대면적 멤브레인을 만들기 위한 것이다. 폭 1m, 길이 24m, 48m에 달하는 멤브레인을 이 장비로 만들 수 있다. 우윤철 박사 안내로 자세한 공정을 접할 수 있었다.
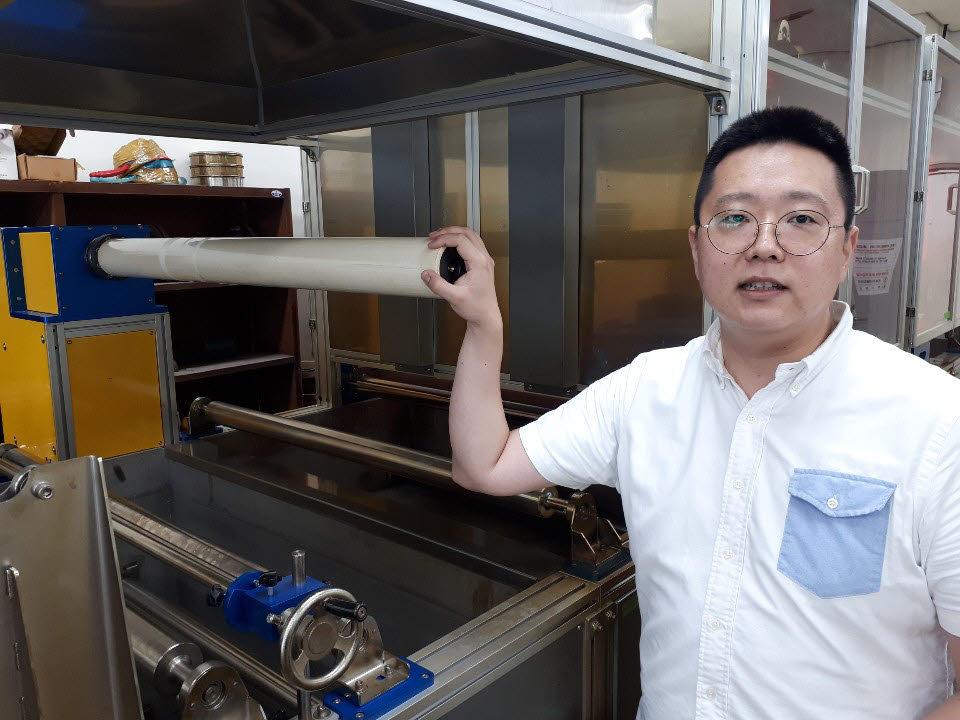
막 제조과정은 아주 복잡했다. 폴리머가 장치 내 챔버들을 거치며 용액에 담궈지기도 하고 열 처리, 건조, 코팅 등 과정을 겪으며 비로소 멤브레인으로 거듭난다. 하루에 4개를 만드는 것이 고작일 정도로 많은 시간이 소요되고, 그만큼 노력도 든다.

연구팀은 그래서 이 일에 자부심과 보람을 느낀다고 했다. 연구실은 이미 해수담수화 관련 10년 연구 업력을 갖추고 있다. 부산 기장에서 1000톤 규모 플랜트 실증에 참여했고, 내년에는 제주에서 100톤 규모 공정·소재 실증에 나설 계획이다.
일 자체가 갖는 매력이 크다. 최준석 위원은 “멤브레인 제작은 정형화되지 않은 시도를 하는 과정에서 뛰어난 결과를 얻게 된다”며 “마치 예술같다”고 전했다.
연구 의의도 일에 빠져드는 이유다. 그는 “해수담수화는 우리 국민의 물 복지에 큰 도움이 된다”며 “하수처리나 발전 등 다양한 분야와도 연계 가능해, 이를 연구하는 것에 큰 책임감을 느낀다”고 말했다.
대전=김영준기자 kyj85@etnews.com