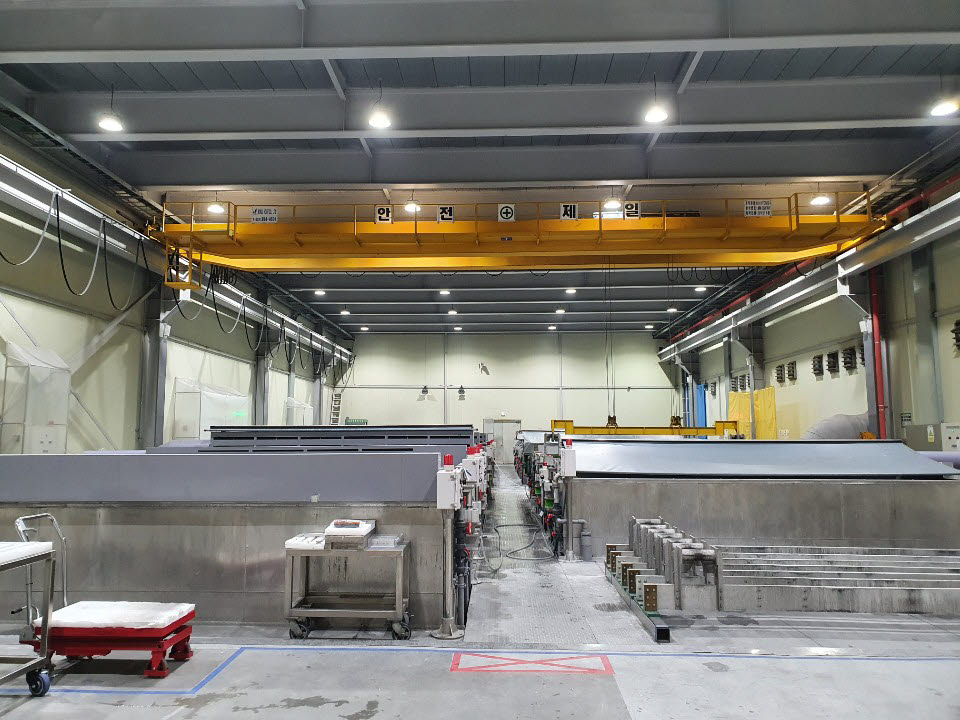
“티티에스 천안사업장에 갖춰진 핵심 표면처리 시스템은 회사 독자 기술로 만들어졌습니다.”
26일 반도체·디스플레이 장비용 부품업체인 '티티에스' 천안사업장에서 만난 임유동 대표는 자사 표면처리 기술에 대한 자신감이 남달랐다.
충남 풍세산업단지 내에 위치한 천안사업장은 후공정 작업이 주로 이뤄진다. 이곳에서는 일정한 간격으로 배치된 수십대 배스(Bath)가 바쁘게 가동되고 있었다.
5m 깊이 배스는 말 그대로 '욕조' 같다. 화학물로 가득 채워진 배스에 전공정을 거친 서셉터라는 부품을 담궈 전기 작용을 일으키면, 부품 표면과 화학물이 반응해 일정한 두께의 피막이 생긴다. 이러한 표면 처리 작업은 아노다이징이라고도 한다.
티티에스는 국내 최초로 디스플레이 장비용 부품에도 대응 가능한 '대면적 장벽형 아노다이징' 기술로 차별화에 성공했다.
서셉터는 디스플레이 패널 제조 장비 안에서 패널에 열을 가하는 역할을 하는 부품이다. 열을 가하면서 고온과 플라즈마 상태에서도 부식되지 않는 것이 중요한데, 아노다이징으로 피막을 씌우면 내구성이 훨씬 강해진다.
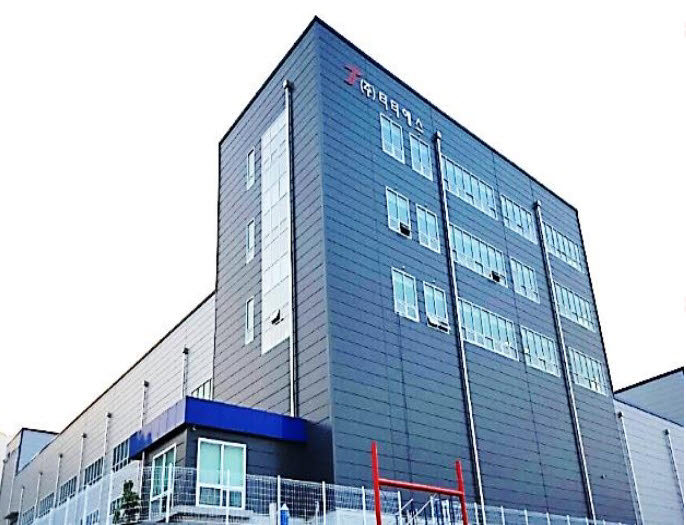
2750평 규모 천안사업장 안에는 피막 작업을 기다리는 서셉터를 곳곳에서 발견할 수 있었다.
그런데 이곳에는 신규 서셉터만 있는 것이 아니다. 국내 각 디스플레이 제조사에서 이미 활용됐던 서셉터를 다시 새것처럼 만드는 재활용 작업도 진행된다. 티티에스는 주력인 서셉터 외에도 디퓨저, 프레임, 정전척 등 다양한 부품에 후공정 작업을 진행해 튼튼하고 정교한 제품을 만든다.
실제 이날 방문한 공장에서는 서셉터 외 핵심 부품인 디퓨저의 미세한 구멍에 먼지가 없는지 꼼꼼하게 확인하는 기계, 후공정 후 잔여물을 깨끗하고 신속하게 씻어내는 로봇이 분주하게 움직이고 있었다. 후공정이 끝난 다음 부품을 모아 제조 장비를 다시 깔끔하게 조립하는 250평 규모 전용 스마트리드 클린룸까지 완비돼 있다.
임 대표는 “신제품 표면 처리는 물론 디스플레이 장비가 묵은 때를 벗겨내고 새롭게 단장할 수 있는 모든 솔루션을 티티에스에서 제공하고 있다”고 설명했다.
티티에스는 2010년 표면처리 분야에 진입한 뒤 2016년 천안사업장을 구축하며 표면 처리 자체 경쟁력 확보에 주력하고 있다. 서셉터 외 디스플레이 및 반도체 장비 부품 표면처리 매출이 전체의 60%를 차지할 정도다.
이제 티티에스는 천안사업장으로 제조 역량을 결집하려고 한다. 본사가 있는 화성사업장의 제조 설비를 천안으로 옮겨와, 올해 안에 부품 전공정과 후공정 및 재활용까지 원스톱으로 해결할 수 있는 최신 설비를 가동하는 것이 목표다.
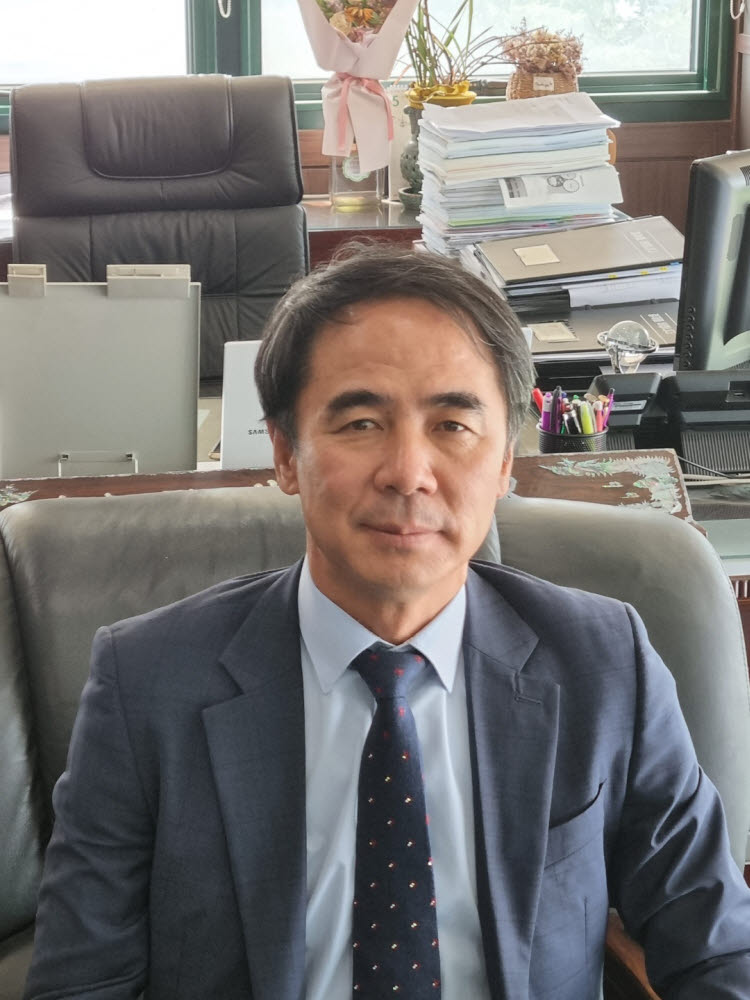
임 대표는 “현재 디스플레이 서셉터 장비뿐 아니라 반도체 장비에 활용되는 알루미늄나이트라이드(AlN)도 개발·생산하며 매출 다변화에 박차를 가하고 있다”며 “반도체·디스플레이 공정장비 핵심 소모성 부품 전문 제조사로 거듭날 것”이라고 강조했다.
천안=
강해령기자 kang@etnews.com