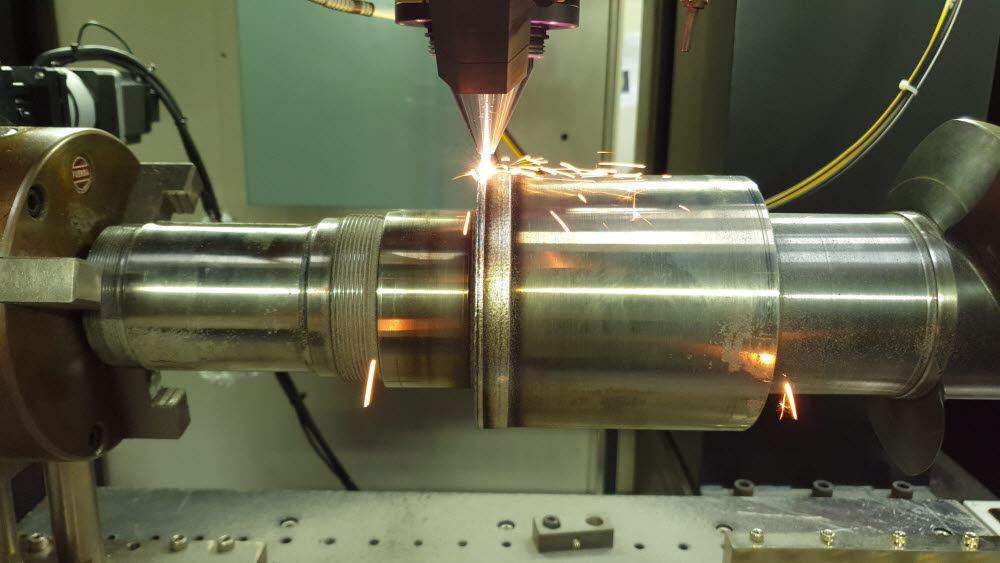
한국생산기술연구원(원장 이낙규)은 금속 3D프린팅 기술로 해군 주력 함정의 동력계 핵심부품인 '감속기 주축'을 보수하고, 이를 함정에 다시 장착해 1년 6개월간 해상에서 정상 운용하는데 성공했다고 18일 밝혔다.
손상됐던 감속기 주축은 고속으로 돌아가는 엔진 속도를 낮춰주고 토크를 제어하는데 그만큼 진동이 잦고 하중을 크게 받아 결함이 발생하기 쉬운 부품이다. 길이가 1.8m에 달하는 대형 부품이라서 신규 주문제작 시 6개월 이상 기간이 소요되고 비용도 6000만원가량으로 고가다. 조속한 임무 복귀를 위해 3D프린팅을 활용한 맞춤형 긴급 보수가 절실한 상황이었다.
생기원 스마트제조기술연구그룹 성지현·이호진 연구원팀은 안석 해군정비창 사무관팀과 함께 2020년 1월 금속 3D프린팅 기술 중 하나인 'DED' 공정을 활용해 결함 부위에 이종 소재를 적층하는 방식으로 부품 보수작업을 단기간에 완료해냈다.
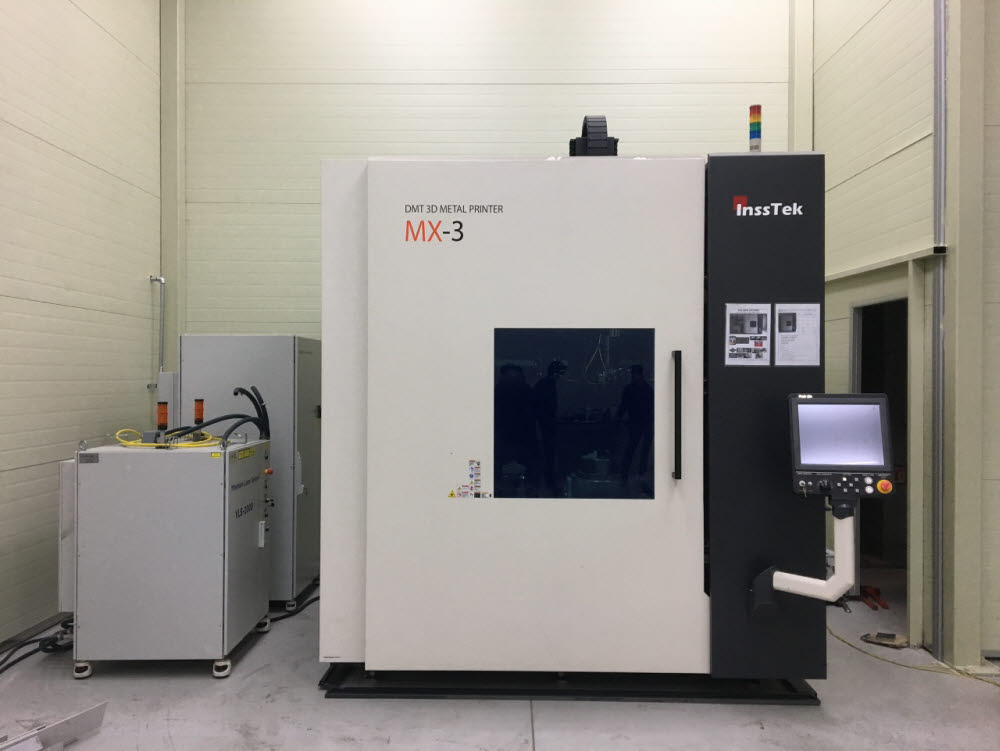
DED 공정은 레이저 빔을 부품 표면에 선택적으로 쏘아 금속 분말을 녹여 쌓는 방식이다.
생기원의 DED 기반 보수기술에는 2016년 3D프린팅제조혁신센터 설립 이후 쌓아온 3D 적층설계, 공정 최적화, 물성평가 분야 기술과 노하우가 집약돼 있다. 동력계 대형부품 보수에 적용된 것은 국내 최초 사례다.
보수된 감속기 주축은 함정에 장착돼 1년 6개월 동안 운영 평가를 받고 있으며, 현재까지 어떤 결함도 발생하지 않고 있다.
수리기간의 경우 주문제작과 비교해 6분의 1 수준인 1개월로 줄였고, 비용도 20분의 1 수준이다.
해군에서는 이달 내로 보수부품에 대한 부대 운영 평가를 완료하고 품질보증 심의까지 마무리 짓는다는 계획이다. 적용 기술을 비상정비 상황에서도 유용한 현장 보수기술로 평가하고 있다.
이호진 연구원은 “이번 사례는 3D프린팅 보수기술의 현주소와 뛰어난 신뢰성을 보여주는 대표사례로, 기존 하우징 부품에 국한됐던 기술의 활용영역을 크게 확장시켜줬다”며 “앞으로 해군 및 국방부와 협력해 단종되거나 조달 애로를 겪는 동력계 부품들을 대상으로 다양한 추가사례를 지속적으로 발굴해나갈 예정”이라고 말했다.
대전=김영준기자 kyj85@etnews.com