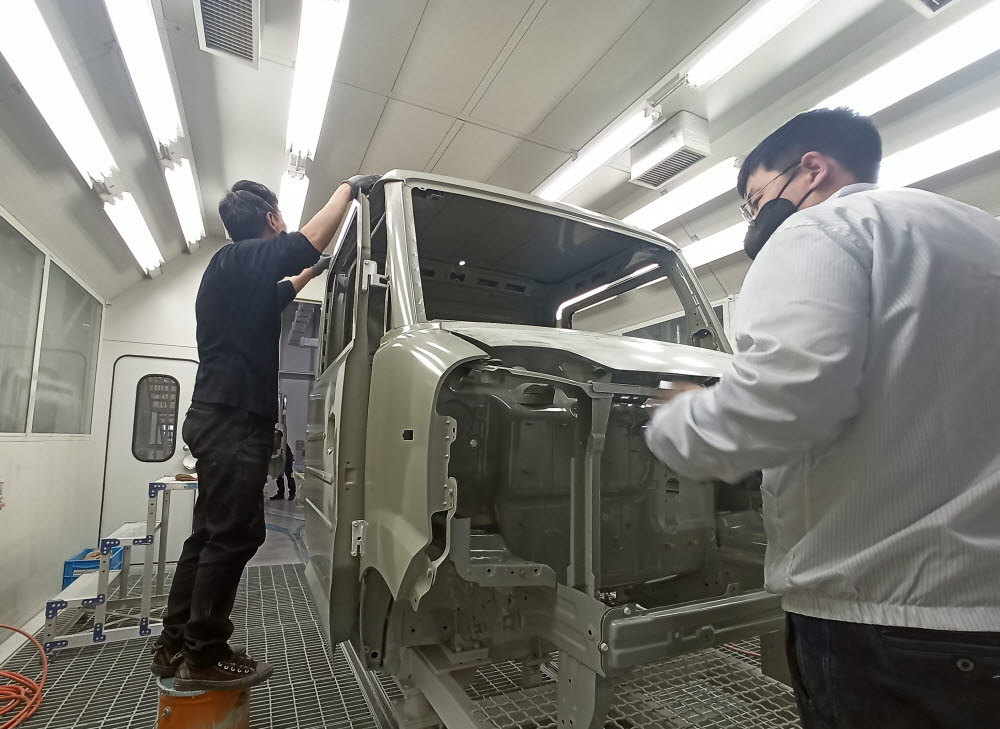
강원도 횡성군 우천산업단지에 위치한 디피코 공장은 경쟁사 공장과 달리 여러 설비로 꽉 차 있었다. 수입한 차에 배터리 등을 추가 조립하는 방식이 아니라 자체 개발한 차량을 직접 생산하기 때문이다. 송신근 디피코 대표는 공장을 소개하며 “현대차를 제외한 국내 전기차 업체 중 차체·도장·조립 공장을 갖춘 곳은 디피코가 유일하다”고 강조했다.
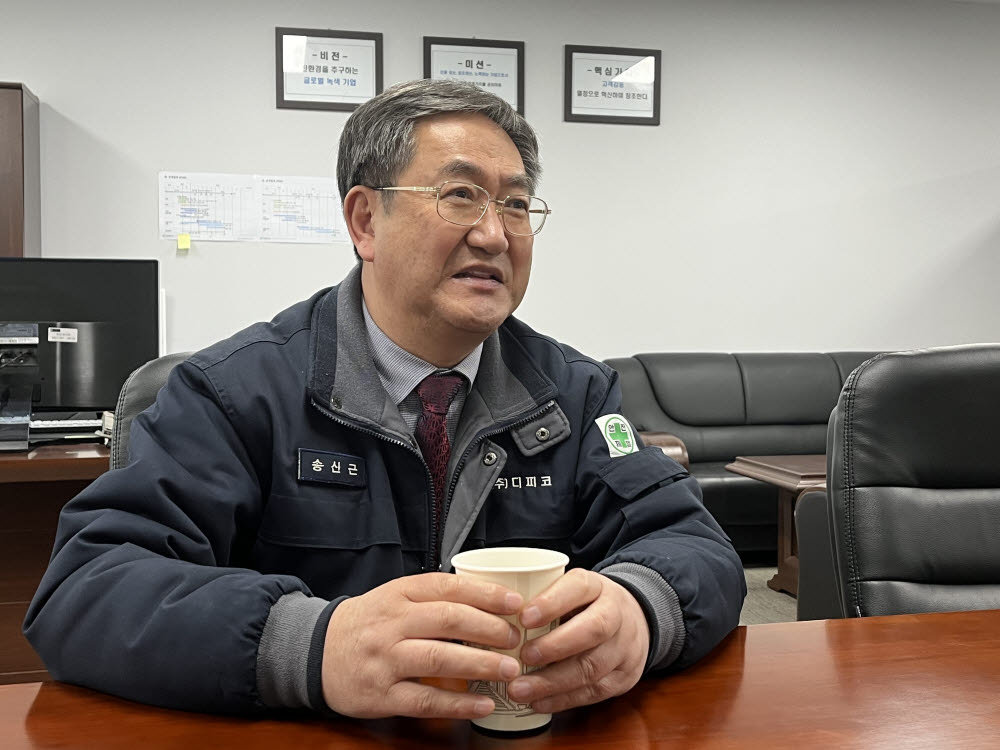
송 대표도 과거 중국 자동차 수입해 국내 판매하는 방안을 검토했다. 하지만 해외 업체에 휘둘리면 안 된다는 생각으로 자체 개발을 택했다. 횡성 우천산업단지가 전기차 생산에 최적지라고 판단해 공장을 착공했고 작년 6월 가동을 시작했다.
지난 25일 방문한 디피코 공장은 차체, 도장, 조립 3개 공장으로 나뉜다. 차체 공장에 들어서자 바닥에 늘어선 부품이 눈에 들어온다. 차체를 구성하는 세부 부품이다. 천장에 매달린 스팟 용접 설비를 거치면서 서서히 차체 모양을 갖춰나간다. 아직 작업은 대부분 반자동으로 이뤄지고 첨단 자동화 로봇은 2대뿐이다. 송 대표는 추가 투자로 모든 설비를 자동화할 계획이라고 설명했다.
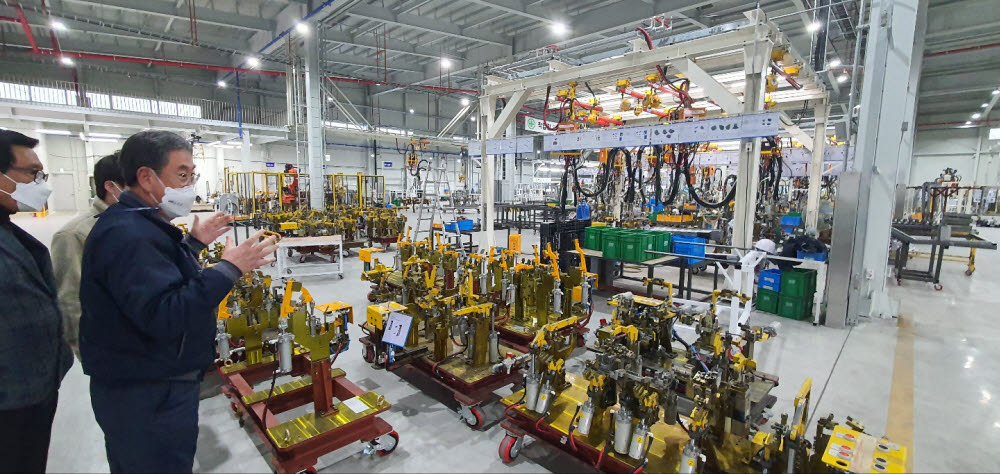
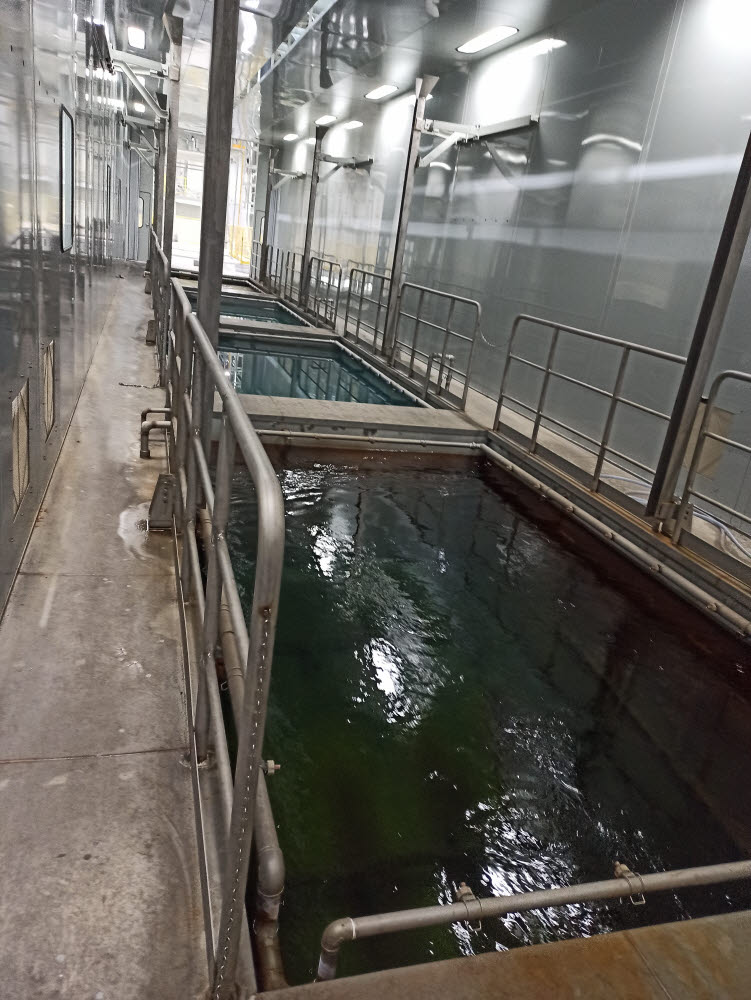
이곳에서 만들어진 차체는 연결된 도장공장으로 옮겨진다. 도장공장은 페인트가 굳지 않도록 24시간 가동해야 한다. 24시간 가동할 생산물량을 확보하기 전까지는 비용 부담이 크지만 내재화했다.
차체는 유분과 불순물을 제거하는 전처리 공정을 지나 도료에 담그는 방식의 전착 공정으로 넘어갔다. 이어 표면을 균일하게 잡아주고 누수 방지 작업, 차체 하부 녹방지를 위한 코팅작업을 거쳤다. 실제 차량 색상을 입혀지는 상도 도장은 이후에 수작업으로 진행됐다.
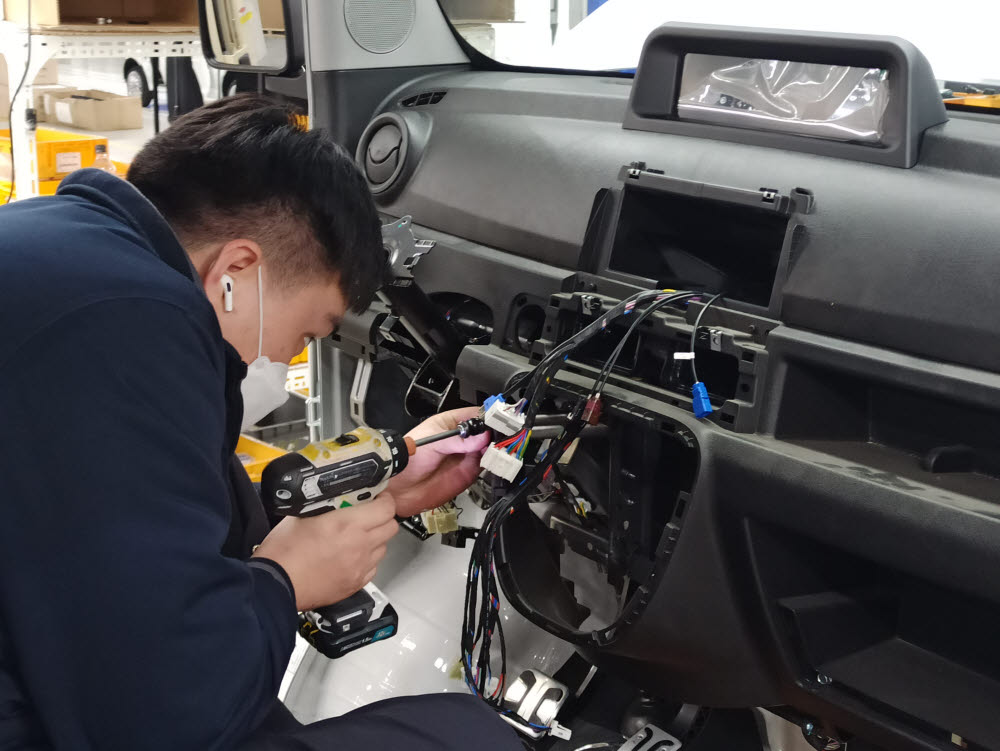
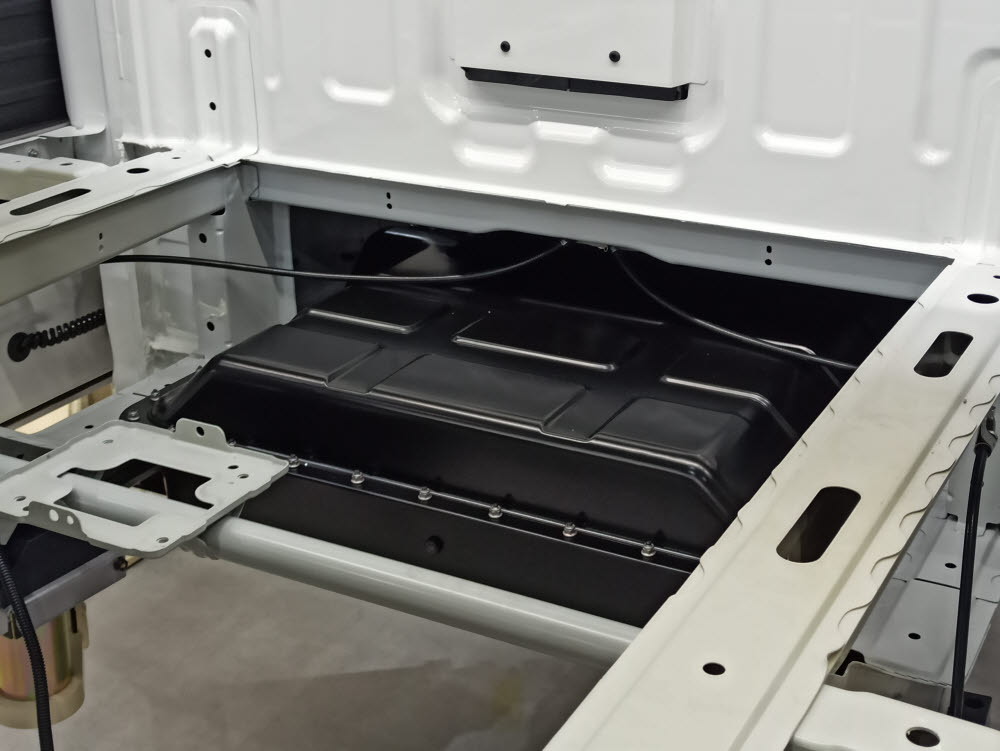
조립 공장에서는 차체에 섀시, 배터리, 타이어 등의 부품이 장착돼 차량 모습을 완성했다. 배터리는 부품 중 가장 무게가 많이 나가지만 작업자들은 특별히 고안한 리프트 기계로 손쉽게 장착했다. 기존 대기업 완성차 제조사 공장과 비교하면 부족하지만 중국 차량을 수입해 단순 조립만 하는 공장과는 격차가 커 보였다.
횡성공장의 연간 생산능력은 2만대다. 디피코는 올해 5000대, 내년 1만대 생산 목표다. 현재 차체공장에서 처리하는 세부 부품 조립은 외부 협력업체에 맡겨 생산효율을 높일 계획이다. 수입 부품이 적어 부품 조달에 따른 생산 차질 걱정도 없다. 부품 국산화율은 85%에 달하며, 연내 90%까지 끌어올린다는 구상이다. 국내 전기차 업계 최고 수준이다.
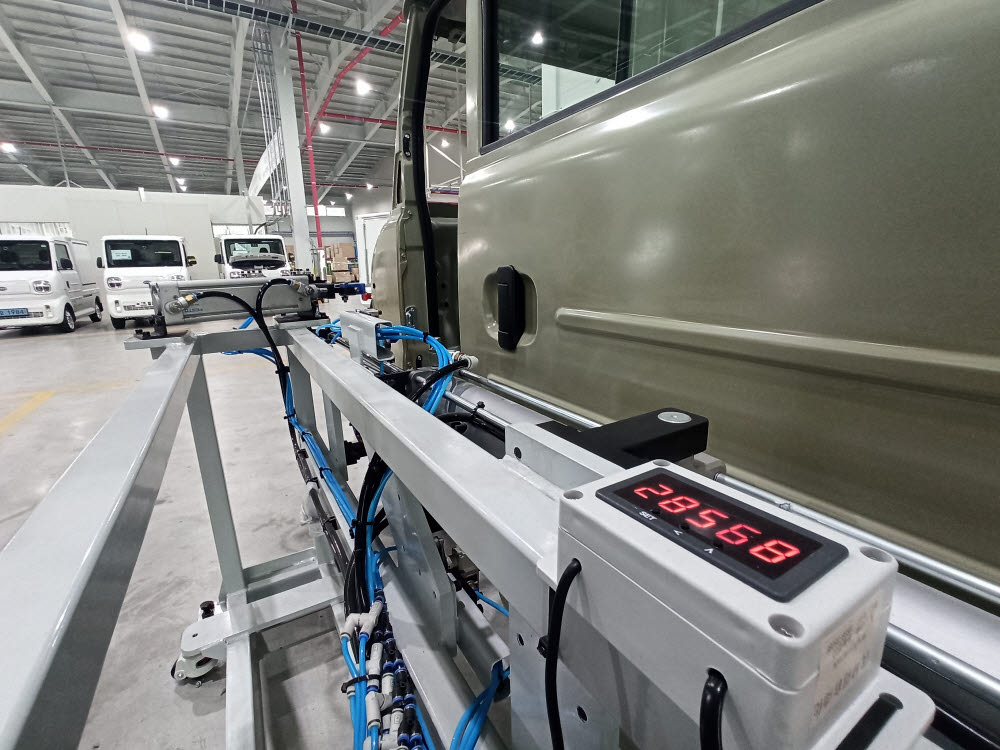
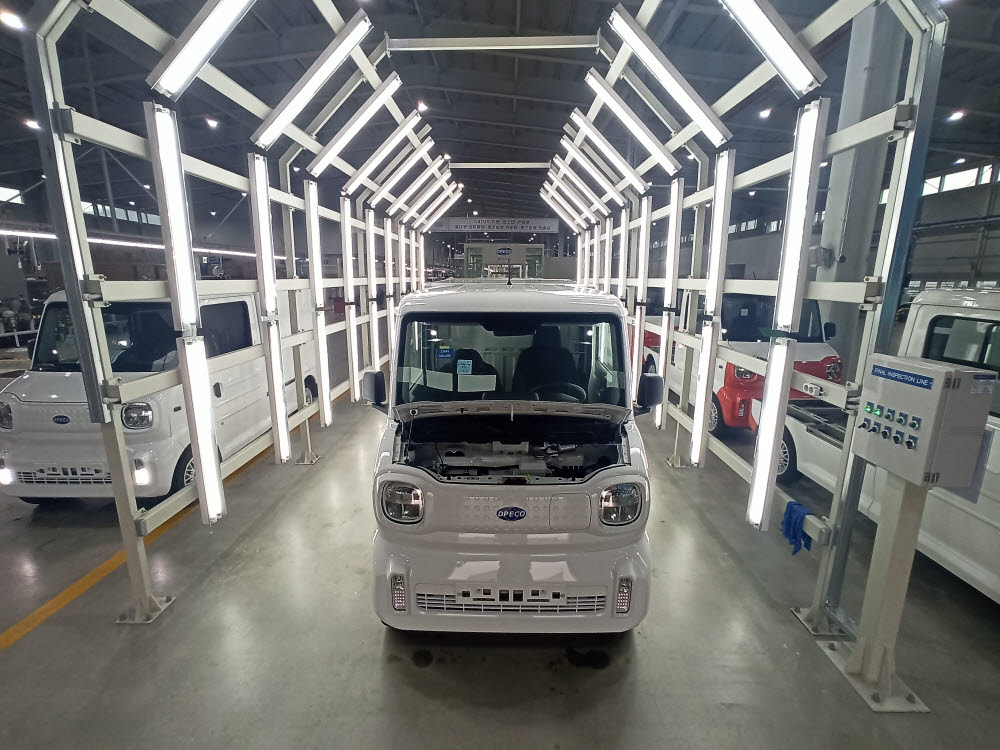
다양한 업계로부터 수요를 발굴해 생산물량을 확보하는 것은 과제다. 디피코는 이를 위해 생산 모델을 다양화한다. 초소형 전기차 '포트로 P250'에 이어 올해 경형 전기차 '포트로 P350'을 출시한다. 최고속도가 기존 70㎞/h에서 100㎞/h로 높아지고 고속도로를 포함한 자동차 전용도로 진입이 가능해져 수요가 늘어날 것으로 예상한다. 주행거리도 최대 278㎞를 지원한다.
송 대표는 “물류·배송 업체와 각종 방문 서비스 업체 등을 공략할 계획으로 B2B로 공급할 원격 차량 모니터링·관제 시스템(FMS)까지 개발을 마쳤다”면서 “국내뿐 아니라 유럽 수출을 위한 인증 절차도 밟고 있다”고 말했다.
박진형기자 jin@etnews.com