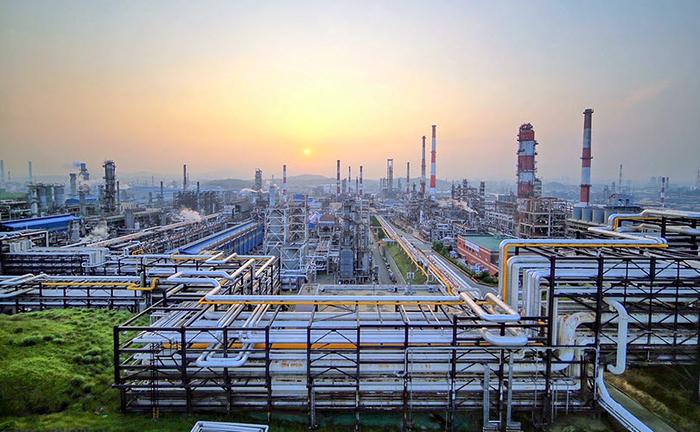
SK이노베이션이 생산, 설비 공정에 인공지능(AI), 디지털 트랜스포메이션(DT) 기술을 적용하며 '스마트 플랜트 2.0' 추진에 속도를 내고 있다. 또 생산 공정에 로봇개를 투입하고 가상현실(VR) 기술을 적용해 보안과 안전에도 DT를 적용한다.
23일 찾은 SK이노베이션 울산 콤플렉스(CLX)에는 '스마트 플랜 2.0' 추진 작업이 한창이었다. 스마트 플랜트는 SK이노베이션이 2016년 국내 석유·화학업계 최초로 도입한 개념이다.
스마트 플랜트는 스마트 팩토리와 생산형태, 규모, 범위 등에서 차이가 있다. 일례로 스마트 팩토리가 제조업을 중심으로 하는 개념이라면 스마트 플랜트는 원료가 변환되는 설비 및 공간을 지칭하며 최종제품 생산단계 이전 중간 생산활동을 포괄한 개념이다.
SK이노베이션은 지속가능한 글로벌 톱티어 경쟁력 확보를 위한 돌파구 전략으로 스마트 플랜트를 추진했다. 올해부터는 AI, DT 기술을 접목해 효율성이 대폭 개선하기 위한 스마트 플랜트 2.0를 추진하고 있다.
SK이노베이션은 공정운전, 설비관리, SHE(안전·보건·환경) 분야에 AI와 DT를 적용한 40여개 스마트플랜트 2.0 과제를 SK 울산CLX에 적용하고 있다고 설명했다.
구체적으로 공정운전 분야의 경우 공정 자동 운전 프로그램을 적용했다. 생산성과 에너지 효율을 최적화하기 위한 공정 자동 제어(APC) 기술에 AI를 도입했다. 과거 운전원들이 직접 조작해야했던 작업이었지만 AI 솔루션을 도입함으로써 생산과 효율성을 높일 수 있다.
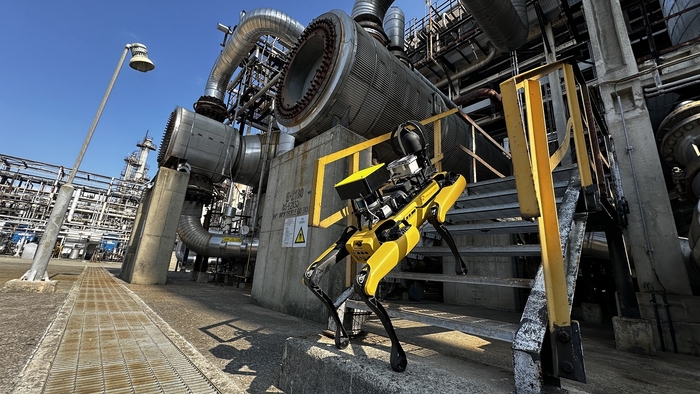
설비의 경우 SK이노베이션이 개발한 '옵션허브' 플랫폼을 통해 관리된다. SK이노베이션 울산 CLX에는 60만개의 공정이 있고 공정마다 설립된 시기도 차이가 크다. 이에 기존의 데이터베이스를 정제하고 현장, 검사, 진단 등 업무도 하나의 플랫폼으로 모았다. 이를 통해 전체적인 모니터링 관리가 가능해졌다.
또 진동 및 온도 등의 설비 데이터 기반 고장 예측 솔루션을 구축했고 드론을 활용한 고소지역 설비 검사, 로봇을 활용한 위험 작업 대체 등을 통해 위험 작업의 로봇 대체 활용을 확대하고 있다.
AI를 적용한 검사 포인트 자동 선정 및 결과 분석, 증강현실(AR)을 활용한 현장 비계 작업 시뮬레이션 및 작업 검증 등 다양한 분야로 영역을 넓혀가고 있다.
정창훈 SK에너지 스마트플랜트 추진팀장은 “AI, DT 기술이 발전함에 따라 전략을 수정할 필요가 있었다”며 “내부적으로는 체계적인 추진을 위해 전담조직을 만드는 등 기존의 계획보다 업그레이드 한다는 의미에서 스마트 플랜트 2.0을 추진하는 것”이라고 밝혔다.
이어 “공정 자동 제어, 설비 고장 사전 예측 등으로 100억원 가량의비용이 절감됐다“고 전했다.
넘버2 FCC공장에는 국내 정유사 최초로 '로봇개'가 도입됐다. 이 로봇개에는 가스탐지기, 열화상 카메라, 30배 줌 카메라 등이 장착됐다.
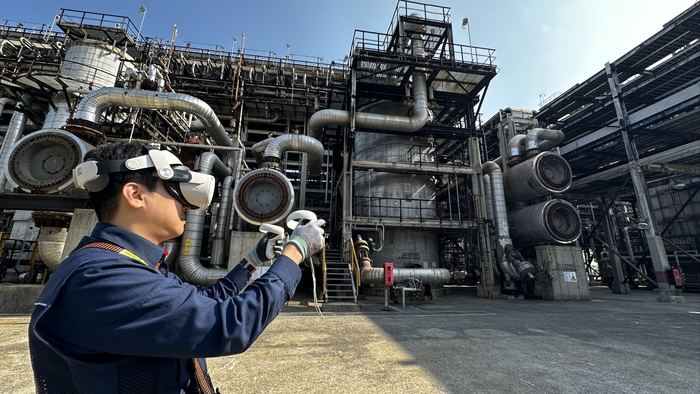
로봇개는 하루 6번, 4~50분가량 순찰을 진행한다. 이때 가스 누출을 발견할 경우, 열화상 카메라를 통해 미리 설정해둔 온도 이상 넘어갈 경우 등이 발생했을 때 중앙관제 모니터링에 알람을 띄운다.
현재 해당 공정에 1마리의 로봇개가 적용됐는데 향후 다른 공정에도 투입할 예정이다.
SK이노베이션 관계자는 “SK 울산CLX는 국내 최초 스마트 플랜트 구축과 운영에 대한 전문성을 바탕으로 최고 수준의 기술을 갖추고 있다”며 “실행력이 한층 강화된 스마트플랜트 2.0을 통해 전세계 최고 수준의 경쟁력을 확보하고 나아가 '자동운전 플랜트'를 추구할 것”이라고 말했다.
조성우 기자 good_sw@etnews.com