디스플레이업계가 초박형 기판유리를 놓고 딜레마에 빠졌다. 기술이 빠르게 발전했지만 정작 실제 생산 현장에서는 수율 확보가 순탄치 않기 때문이다. 공급받은 기판 유리를 다시 얇게 깎아내는 슬리밍 공정을 대체해 원가절감 효과가 크지만 수율 문제가 발목을 잡는다. 초박형 기판을 원활하게 사용할 수 있는 공정 기술과 노하우에 대한 업계 관심이 커졌다.
코닝, 아사히글라스 등 주요 디스플레이용 기판유리 제조사는 0.1T(㎜) 두께의 초박형 기판유리를 개발했으나 아직 시장에서 도입하지 않고 있다.
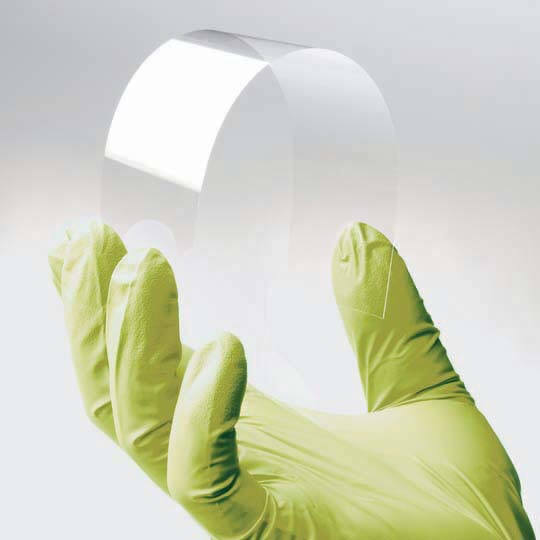
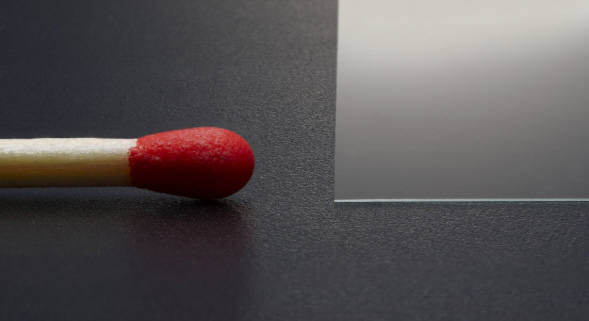
삼성디스플레이가 이례적으로 대형 TV용 기판유리에 0.3T 제품을 도입했으나 기판 깨짐 현상이 발생해 어려움을 겪고 있다. 올 상반기 중으로 문제를 해결할 전망이지만 이전 수준으로 수율을 완전히 회복할지 귀추가 주목된다. 2분기 내 문제를 해결하더라도 새로운 기판 유리가 안정적인 수율을 내기까지 약 6개월 이상 걸린 셈이다.
초박형 기판유리는 액정표시장치(LCD) 원가절감 효과가 탁월한 것으로 알려져 있다. 패널 제조사는 공급받은 두꺼운 기판유리에 TFT 공정(하판)과 컬러필터(상판)를 입히고 둘을 합착한 뒤 슬리밍 공정을 한다. 초박형 유리를 사용하면 슬리밍 공정을 거치지 않아도 되므로 전체 생산 시간과 비용을 줄일 수 있기 때문이다.
유리 슬리밍은 화학적 용액으로 식각하거나 물리적으로 깎아내는 방식이다. 화학적 식각은 깎아내는 유리 양이 많을수록 식각액 사용량이 늘어나므로 비용이 증가한다. 패널 두께와 무게가 얇아지면 화면 굴절률이 줄어들고 투과율은 늘어나 전체적으로 디스플레이 품질을 높일 수 있다.
삼성디스플레이가 주력하는 커브드 디스플레이처럼 물리적으로 패널을 구부려야 할 때도 초박형 기판이 유리하다. 곡률을 일정하게 유지하려면 상대적으로 쉽게 구부릴 수 있는 얇은 기판유리가 좋다.
문제는 생산 공정 과정에서 발생하는 파손 문제다. 기판유리에 TFT, 컬러필터, 액정주입 등 다양한 공정을 시행할 때 힘이 가해지면서 기판이 깨진다. 0.1T 기판유리는 마치 플라스틱처럼 위아래로 휘어질 정도로 유연성이 있고 강성도 높지만 실제 공정 과정에서 열과 압력에 노출됐을 때 파손될 가능성이 있다.
일각에서는 초박형 기판유리 도입 비용이 기존 슬리밍 공정 유지비용보다 더 높을 수 있다고 분석한다. 기판유리가 얇아지면 플렉시블 유기발광다이오드(OLED) 공정처럼 별도의 캐리어 유리가 필요할 수 있기 때문이다.
플렉시블 OLED는 기판이 휘어지는 특성 때문에 기판을 이동시키기 위한 고정밀 캐리어 유리를 사용한다. 패널 제조사 입장에서는 슬리밍 공정을 없애더라도 캐리어 유리를 사용하기 위한 공정을 추가해야 하므로 추가적인 유리·공정 비용이 들 수 있다는 지적이다.
한 관계자는 “기판유리 두께가 0.2T 수준이면 별도 캐리어 유리가 필요할 것”이라며 “공정 단계 중 기판이 파손되는 수율 문제까지 감안하면 초박형 유리 도입은 앞으로도 계속해서 업계 딜레마가 될 것”이라고 말했다.
반면에 슬리밍 공정을 없애는 것이 전체 시간·비용 절감에 탁월하다는 시각도 여전하다. 슬리밍 공정에 필요한 화학액 공급장치, 재활용 장치, 폐수처리시스템 등 관련 설비 운용비용과 지속적으로 필요한 재료비를 감안하면 도입 기회비용을 감수하더라도 원가절감 효과가 크다는 주장이다.
한 관계자는 “더 얇고 튼튼한 제품을 만들기 위해 초박형 기판유리가 필요하므로 관심과 수요가 늘고 있다”며 “궁극적으로 미래 롤투롤 공정으로 진화하는 과정이므로 초박형 유리 수요는 지속적으로 커질 것”이라고 내다봤다.
배옥진 디스플레이 전문기자 withok@etnews.com