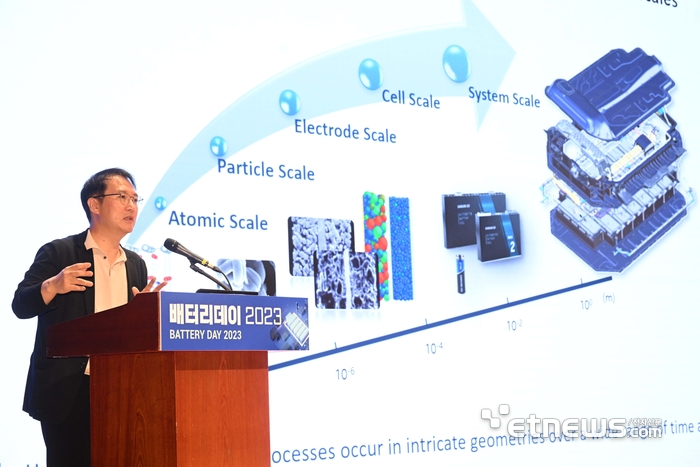
삼성SDI가 인공지능(AI)·빅데이터 분석 기술을 활용해 배터리 연구개발(R&D) 단계에서 성능을 미리 예측하고 확인하는 기술 개발에 나섰다.
기존에는 작은 외부 환경 변화나 시간 흐름에도 영향을 받는 배터리 특성상 시제품 또는 완제품이 나와야 성능 테스트가 가능했다.
완제품의 기술적 결함이 확인되면 원인을 파악하고 다시 개발하는 방식을 반복해야 해 R&D부터 배터리 생산까지는 오랜 시간이 소요됐는데, 이를 극복하는 것이다.
김기헌 삼성SDI 부사장은 전자신문 주최 ‘배터리데이 2023’에서 “배터리 R&D의 어려움 중 하나가 완제품이 나와야 성능을 확인할 수 있다는 점”이라며 “삼성SDI는 공정 인자·설계 인자 등 다양한 조건을 고려하고 그동안 축적된 데이터를 분석, 배터리 개발·생산 중간과정에도 반제품 품질로 배터리 최종 성능을 예할 수 있는 기술을 고도화하고 있다”고 소개했다.
방법은 이렇다. 배터리 개발 단계를 공정 단위별로 모듈화하고 배터리 R&D·생산·테스트 관련 축적된 데이터를 기계학습, 단계별 산식을 수립했다. 반복적인 머신러닝으로 재료·설계가 배터리 성능에 미칠 수 있는 영향에 대한 데이터를 수집·분석하고 원자, 물질, 전극, 셀, 시스템 등 배터리 개발 단위별 설계와 여러 단위가 조합된 설계가 배터리 성능에 어떤 영향을 미치는지 확인·예측하는 다양한 산식을 만드는 것이다.
김 부사장은 “정확한 배터리 성능 예측 값을 얻기 위한 실험을 반복하고 데이터를 확보해 분석하고 있다”면서 “배터리 연구·생산 중간 단계에서 성능 검사결과와 최종 제품이 나왔을 때 성능 검사결과 간 차이를 최소화하는 단계에 있다”고 전했다.
삼성SDI는 배터리 재료 디자인부터 매크로 스케일 등 디바이스 레벨 반응까지 이해하고 연결·확인할 수 있는 모델을 개발했다. 소재에서부터 디바이스까지 배터리 R&D를 진행하는 동안 생산되는 설계, 제작공정, 평가 관련 데이터를 연계해 축적하고 데이터베이스(DB)화해 성능 예측에 대한 인텔리전스를 확보했다고 밝혔다.
단, 배터리의 복잡한 특성으로 최종 성능을 예측하긴 쉽지 않아 이론 모델까지 함께 고려해야 한다고 강조했다. 이론과 데이터에 기반한 가상 시뮬레이션을 통해 배터리가 최종 개발됐을 때를 가정, 성능값을 미리 추론·예측해야 한다고 김 부사장은 설명했다.
전극 단위를 예로 들면 배터리 개발단계에서 활용한 데이터에 기반해 버추얼 공간에 배터리 전극 구성을 구현한다. 미세구조상에서 정교한 성능 비교로 어떻게 전극을 구성해야 배터리에 최적화되고 가장 이상적인 성능의 배터리가 생산될 수 있는지를 확인하는 방식이다. 이러한 작업의 정확도가 올라가면 배터리 설계단계에서 최종 배터리 성능을 예상, 최적화된 설계도를 확보할 수 있을 것으로 기대된다.
김 부사장은 “제약과 바이오 분야에서는 이미 많이 활용되고 있는 기술로 배터리 분야에서는 이제 막 시작하는 단계”라며 “배터리에 적용이 더뎠던 이유는 복잡한 배터리 특성상 정확한 결과값을 얻기 위해 많은 양의 복잡한 계산이 필요했기 때문”이라고 말했다.
리튬이온 배터리는 살아있는 생물체에 비유될 정도의 물리·화학적 독특한 특징을 가져 환경 요인에 따라 성능이 달라져 예측에 근본적 어려움이 있다. 배터리는 단독 소재뿐 아니라 다양한 소재를 결합하는 경우도 많은데 이 경우에는 완제품을 생산하기 전에 성능을 예측하기 쉽지 않았다.
김 부사장은 “디지털 트윈 기술을 활용해 배터리의 예측 수명을 실시간으로 확인하는 모델도 개발하고 있다”며 “첨단기술을 배터리 특성에 가장 적합한 방식으로 활용해 삼성SDI가 배터리 산업 R&D 효율화를 선도하는데 기여하고 싶다”고 강조했다.
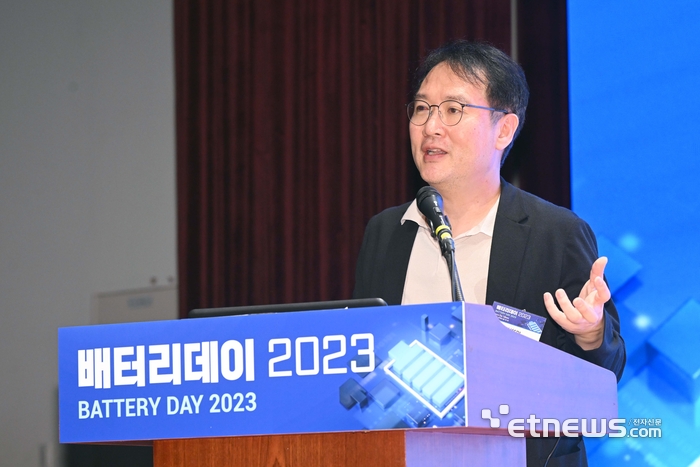
박종진 기자 truth@etnews.com