“완성차 조립 공정에 맞춰 순서대로 모듈을 생산함으로써 재고 관리와 생산 효율성을 극대화하고, 271개 항목에 달하는 엄격한 보증 관리로 완성차 품질 향상에도 일익을 담당하고 있습니다.”
지난 24일 충남 아산시 영인면에 위치한 현대모비스 아산모듈공장은 무더운 날씨에도 불구하고 생산 라인이 분주히 가동되고 있었다. 각종 작업 지시 모니터와 조립 및 기능 검사 장비 등과 함께 공장 근로자들이 빈틈없이 완성차에 탑재될 모듈을 조립하고 있었다.
지난 2004년 가동을 시작한 아산공장은 현재 HG 그랜저, YF 쏘나타 및 LF 쏘나타에 장착되는 섀시(프런트·리어), 운전석, 프런트엔드 3대 핵심 모듈을 생산한다.
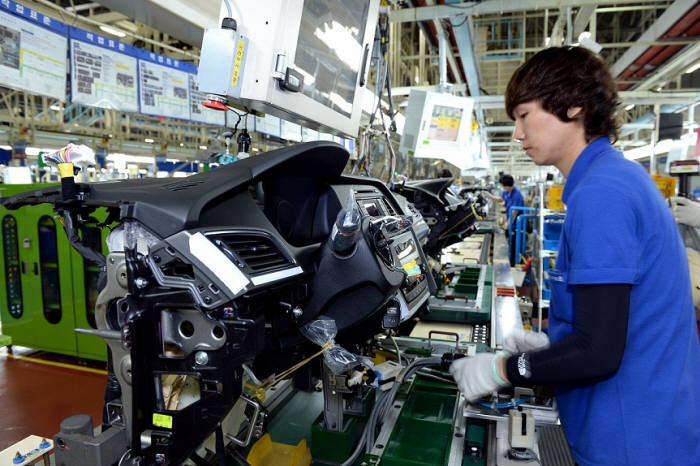
완성차 기준으로 연간 30만대에 달하는 모듈 생산능력을 갖췄으며, 시간당(UPH) 66대 분량의 모듈을 생산한다. 채 1분도 안 되는 시간에 완성차 1대에 들어가는 3대 모듈이 생산되는 셈이다.
현대모비스 모듈공장의 최대 강점은 높은 생산성과 함께 완성차 조립 라인과 완벽하게 연동되는 ‘직서열(Just In Sequence) 생산 시스템’이다. 직서열 생산은 완성차와 동시에 순서대로 모듈을 생산, 필요한 시점에 완성차 라인에 모듈을 공급하는 현대모비스의 첨단 생산 시스템이다. 부품업체와 완성차 업체가 생산 현황을 실시간 공유하고 이를 바탕으로 적기에 모듈을 공급함으로써 재고 부담을 낮추고 완성차 공정 최적화도 용이한 것이 특징이다.
공조 시스템, 에어백 모듈, 오디오 등 총 44개 부품으로 이뤄진 운전석 모듈의 경우, 조립부터 12㎞ 떨어진 현대차 아산공장 납품까지 총 85분이 걸린다. 완성차 생산 개시 이후 운전석 모듈 조립이 이뤄지는 리드타임(101분)까지 16분의 여유시간이 생기는 식이다.
모듈 생산단계의 엄격한 품질 보증 및 관리 시스템도 돋보인다. 부품 조립단계에서 다른 부품이 조립되는 것을 방지하는 이종방지 104개 항목을 비롯해 기능검사(64항목)와 체결보증(103개소)까지 총 271개 항목의 검사가 이뤄진다. 특히 각 시스템에 축적된 생산 이력은 최소 23년 간 통합 관리됨으로써 모듈 품질 향상 데이터로 이용된다. 실제 현대모비스의 모듈화 사업이 정착되면서 현대자동차의 품질 문제가 절반 이상 감소하는 성과를 거두기도 했다.
이영기 경인모듈생산실장은 “아산모듈공장의 불량 건수는 10만대당 1~2건 미만으로 사실상 불량률 제로로 평가할 수 있다”며 “강력한 품질보증 시스템으로 불량을 미연에 방지하고, 입고되는 부품의 전수검사를 실시하는 등 품질 확보에 만전을 기하고 있다”고 말했다.
아산=
양종석기자 jsyang@etnews.com